Yarn engineering focuses on the development and production of yarns, the fundamental building blocks of textiles. This specialized field is crucial for creating fabrics with specific characteristics, including strength, elasticity, texture, and color. The integration of 3D printing into yarn engineering has opened up innovative avenues for manufacturing yarns with complex designs and functionalities that traditional spinning and twisting techniques cannot achieve. As 3D printing technology continues to evolve, it offers significant potential to transform the yarn industry by enabling the production of engineered yarns that can be used in a wide range of applications, from fashion to industrial textiles.
The Emergence of 3D Printing in Yarn Engineering
Initially used for prototyping and small-scale manufacturing in various industries, 3D printing has expanded its applications to include textile manufacturing, particularly in the engineering of yarns. This technology allows for precise control over the yarn’s structure, composition, and properties, enabling the creation of yarns that are tailored for specific functions and performance requirements. As 3D printing technologies advance, they provide new tools for yarn engineers to experiment with novel materials and complex geometries, pushing the boundaries of what traditional yarns can do.
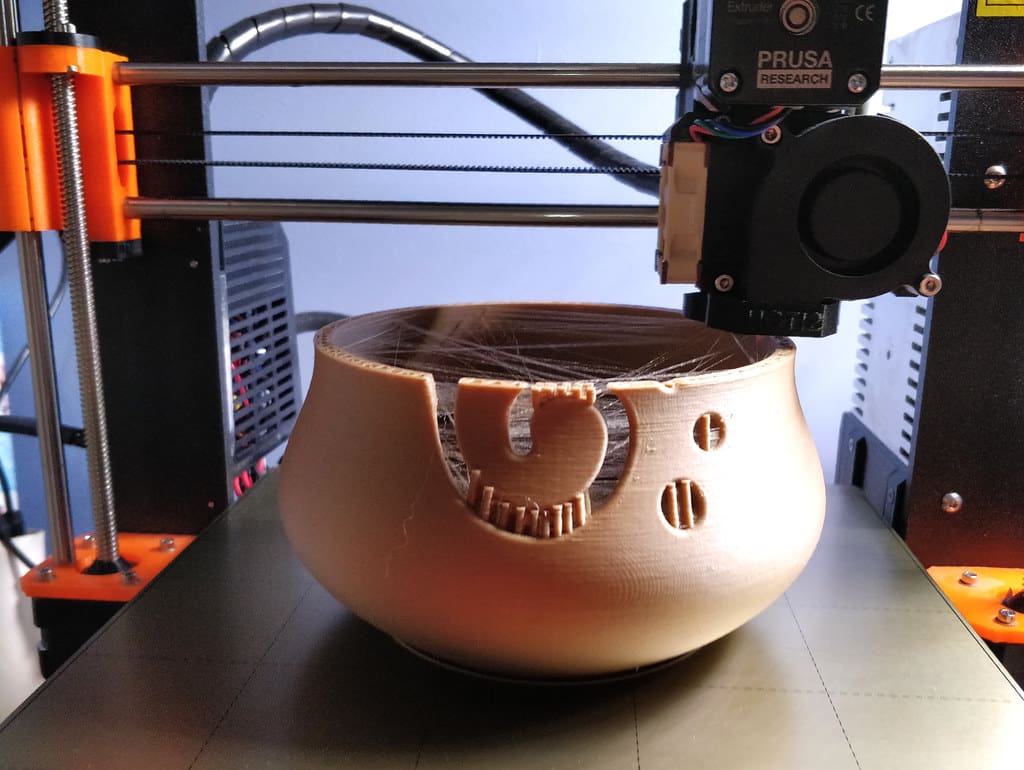
Advantages of 3D Printing in Yarn Engineering
Complexity and Precision: 3D printing allows for the creation of yarns with highly complex structures that are not possible with conventional yarn manufacturing methods. This includes the ability to precisely control the diameter, cross-section, and composition of the yarn throughout its length.
Functional Integration: Through 3D printing, yarns can be engineered to have integrated functionalities, such as conductivity, self-healing properties, or change in color in response to environmental stimuli. This opens up new applications in smart textiles and wearable technology.
Customization and Flexibility: Additive manufacturing supports the customization of yarns at no significant additional cost or production time. This is particularly valuable in high-performance sectors such as sports and medical textiles, where material properties can be optimized for specific applications.
Sustainability: 3D printing can potentially reduce waste in yarn production by using exact amounts of material needed to build the yarn, unlike traditional methods that may generate excess waste during spinning and dyeing processes.
Key Applications of 3D Printing in Yarn Engineering
Smart Textiles: By embedding sensors and electronic components directly into yarns, 3D printing can create smart textiles that monitor health metrics, adjust to temperature changes, or even harvest energy from the wearer’s movements.
High-Performance Sports Wear: Engineered yarns can be produced to provide specific attributes such as enhanced moisture management, improved thermal properties, or increased durability, crucial for sports apparel.
Medical Textiles: 3D printed yarns are used in medical textiles to create customized implants, sutures, and bandages that conform precisely to patient needs and promote faster healing.
Composite Reinforcement: In automotive and aerospace industries, yarns engineered for specific structural properties can be used to reinforce composites, enhancing their strength and reducing their weight.
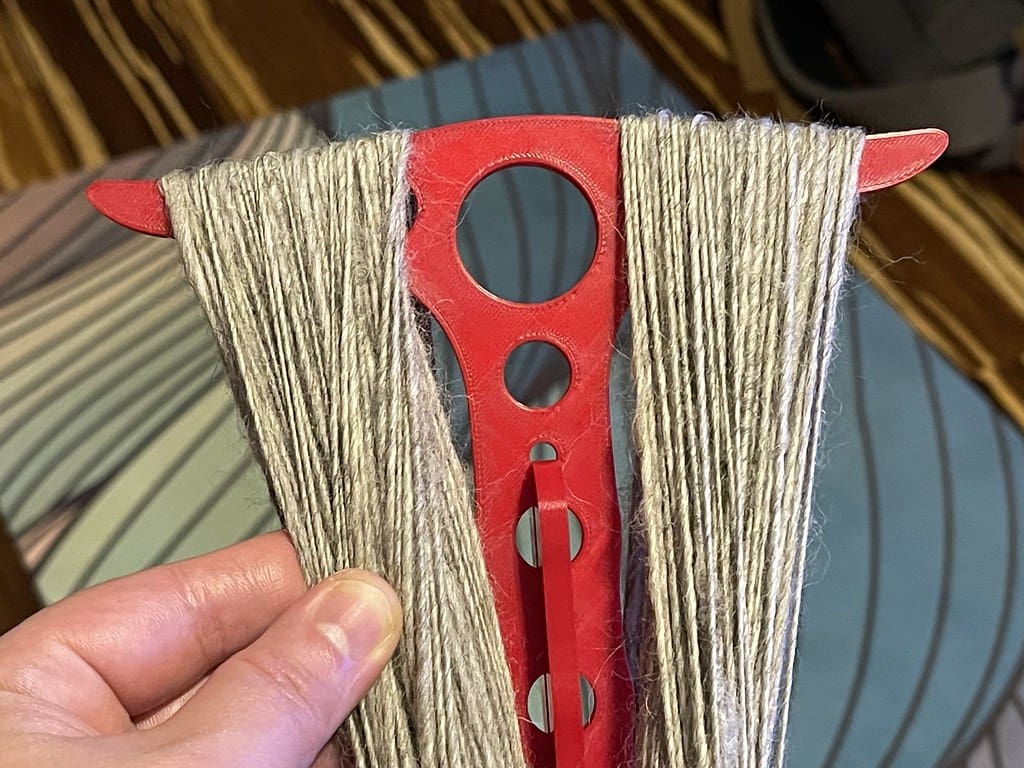
Challenges in 3D Printing for Yarn Engineering
Material Limitations: The range of materials suitable for 3D printed yarns is still evolving. Extending this range to include more fibers that mimic the properties of natural yarns is crucial for broader application.
Production Speed and Scalability: While 3D printing offers excellent precision and customization, the speeds currently achievable are generally lower than those of traditional yarn manufacturing processes, posing a challenge for mass production.
Technical Complexity: Integrating 3D printing into existing yarn production lines requires overcoming significant technical challenges, including the adaptation of 3D printing technologies to handle soft and flexible materials typical of yarns.
Market Acceptance: Convincing the textile industry and consumers to adopt 3D printed yarns, especially in traditional sectors like fashion, requires demonstrating clear advantages in terms of product performance and cost.
Future Directions in 3D Printing for Yarn Engineering
The future of 3D printing in yarn engineering looks promising, with ongoing research focused on improving the printing techniques for soft materials, expanding the material options, and increasing the production speed. Innovations are expected to enhance the functional capabilities of yarns and open up new markets for 3D printed textiles.
3D printing is poised to revolutionize yarn engineering by providing new methods for designing and manufacturing advanced yarns. As the technology advances, it promises to enhance the capabilities and functionalities of textiles, making significant impacts across various sectors, from fashion to functional textiles. With continued development and integration, 3D printing will increasingly become an integral part of yarn engineering, reshaping how yarns are conceived, produced, and utilized in textile manufacturing.