Power engineering, a critical sector focused on the generation, transmission, distribution, and utilization of electric power, is embracing 3D printing as a transformative technology. This innovative manufacturing approach is reshaping how components and systems within the power sector are designed, developed, and maintained. From renewable energy sources to traditional power plants, 3D printing offers significant improvements in efficiency, customization, and sustainability.
3D Printing in Power Engineering
Initially used primarily for prototyping, 3D printing has expanded its applications to include the production of functional components for the power industry. This includes parts for turbines, cooling systems, and intricate components for nuclear reactors. 3D printing’s ability to create complex geometries and incorporate diverse materials into a single manufacturing process significantly enhances the performance and reliability of power systems.
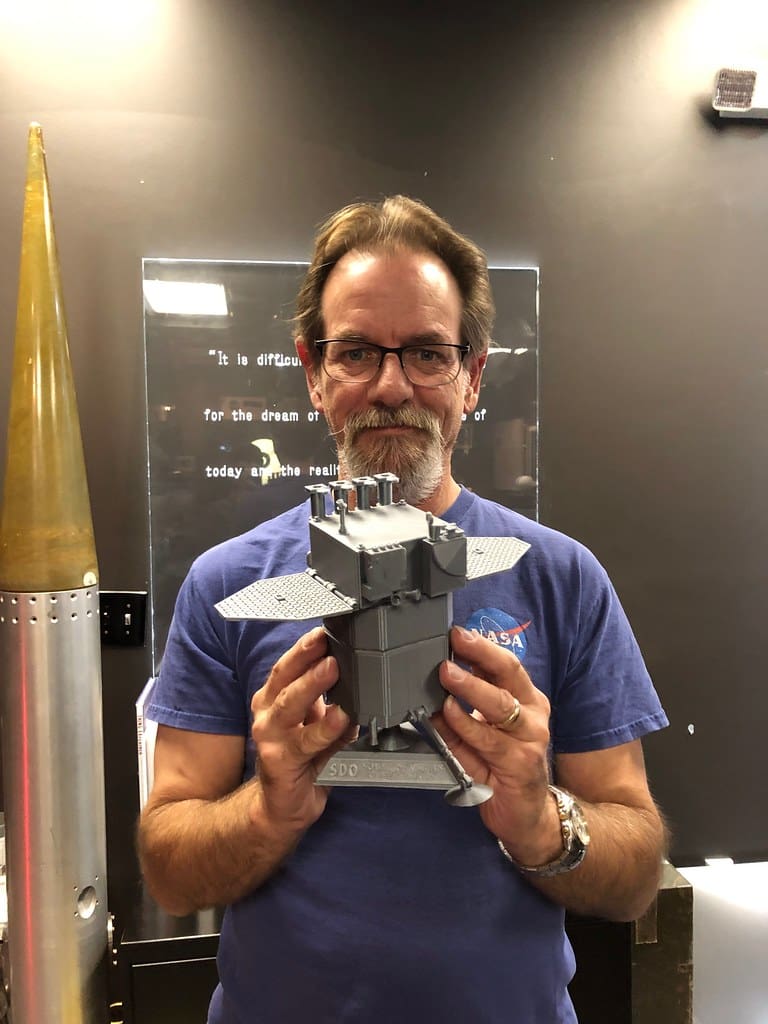
Advantages of 3D Printing in Power Engineering
Enhanced Design Flexibility: 3D printing allows for the creation of components with complex internal structures that traditional methods cannot achieve. This capability is crucial for improving the efficiency and functionality of power generation equipment, such as heat exchangers and turbine blades.
Rapid Development and Innovation: The ability to quickly prototype and test new designs accelerates the innovation cycle in power engineering. Engineers can explore novel concepts for enhancing energy efficiency and environmental sustainability without the constraints of traditional manufacturing processes.
Cost Reduction: By reducing the need for costly tooling and minimizing material waste, 3D printing lowers the overall cost of manufacturing power system components. It also allows for cost-effective small-scale production and custom solutions, which are particularly beneficial in the development of specialized equipment for renewable energy applications.
Sustainability: 3D printing contributes to sustainability in power engineering by optimizing material usage and enabling the production of lighter and more efficient components. Additionally, the ability to use recycled materials further reduces the environmental impact of manufacturing processes.
Key Applications of 3D Printing in Power Engineering
Turbine Components: In both wind and hydroelectric power sectors, 3D printing is used to produce turbine parts that are lighter, stronger, and more efficient. The precise control over material placement allows for the optimization of designs for fluid dynamics and energy conversion efficiency.
Custom Solar Energy Solutions: For solar energy, 3D printing enables the creation of bespoke components for solar panels and mounting systems. These components can be designed to maximize the capture of sunlight in specific geographical locations, enhancing the overall efficiency of solar farms.
Nuclear Power Components: The nuclear sector benefits from 3D printing in the production of custom cooling components and intricate parts that must meet strict safety standards. 3D printing offers the precision needed for these high-specification components, improving the safety and efficiency of nuclear reactors.
Battery and Storage Solutions: As energy storage becomes a crucial aspect of managing power distribution, 3D printing is playing a role in developing advanced battery systems. This includes the creation of battery casings and internals that optimize space and enhance the performance of energy storage units.

Challenges in 3D Printing for Power Engineering
Despite its potential, several challenges remain for the widespread adoption of 3D printing in power engineering:
Material Performance: Ensuring that materials used in 3D printing can withstand the harsh environments of power generation—such as high temperatures, pressure, and corrosive conditions—is essential. The development of new materials that meet these requirements is ongoing.
Scalability: While 3D printing is effective for prototyping and manufacturing small components, scaling up to larger structures, such as entire turbine blades or reactor parts, poses significant technical and economic challenges.
Regulatory and Standards Compliance: The power industry is heavily regulated, and all components must meet stringent performance and safety standards. Integrating 3D-printed parts into critical power infrastructure requires extensive testing and certification to ensure compliance with industry regulations.
Future Directions in 3D Printing for Power Engineering
The future of 3D printing in power engineering looks promising, with ongoing advancements in printer technologies and materials science. Innovations are expected to address current limitations, broadening the applications of 3D printing in this field. Furthermore, as renewable energy solutions continue to grow, 3D printing will likely play a crucial role in developing these technologies by providing flexible, efficient, and sustainable manufacturing options.
3D printing is set to revolutionize power engineering by offering enhanced capabilities for designing and manufacturing complex, efficient, and sustainable components. As the technology continues to evolve, it promises to enable new levels of innovation and efficiency in the power sector, leading to smarter, more sustainable energy systems worldwide.