Multi Jet Fusion (MJF) has emerged as a groundbreaking 3D printing technology developed by HP. This method stands out for its ability to produce high-quality, functional parts at high speeds, making it a favorite in industries that demand both precision and efficiency.
How MJF Printing Works
MJF operates on a sophisticated mechanism that starts with laying down a thin layer of powder material, typically nylon. Instead of using a single laser to sinter the material, MJF utilizes an inkjet array that applies fusing and detailing agents across the powder bed. An energy source, such as infrared lamps, then passes over the layer. The areas with fusing agent absorb more energy and sinter, while the detailing agent helps define crisp edges and fine details by reducing the energy absorbed. This process repeats layer by layer until the entire part is complete, encapsulated within the unsintered powder which supports the item during production without the need for additional structures.
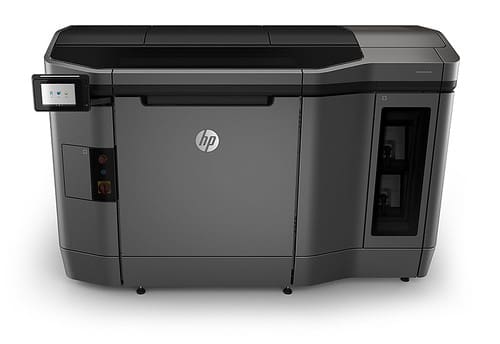
Advantages of MJF 3D Printing
The advantages of MJF are significant:
Speed: MJF is renowned for its quick processing times, capable of printing parts faster than many laser-based systems by sintering entire layers simultaneously.
Detail and Quality: The technology offers excellent detail, precision, and consistency thanks to the controlled application of fusing and detailing agents, making it ideal for complex geometries.
Strength and Durability: Parts produced with MJF exhibit strong and isotropic mechanical properties, meaning they are equally strong in all directions. This makes MJF-produced parts highly functional and suitable for a variety of demanding applications.
Applications of MJF 3D Printing
MJF has been widely adopted across several sectors:
Automotive: For producing durable, complex parts required in short timelines.
Aerospace: For lightweight components that reduce overall aircraft weight without compromising strength.
Healthcare: In the production of customized prosthetic and orthotic devices that benefit from MJF’s ability to tailor products to individual specifications.
Considerations and Limitations
Despite its many benefits, there are considerations to bear in mind with MJF:
Material Limitations: Currently, MJF predominantly uses nylon. Although versatile, ongoing research is necessary to expand the range of materials to include high-performance polymers and composites.
Cost Considerations: The initial investment for MJF technology can be high, although it is often justified by its rapid production capabilities and part quality.
Post-Processing: While parts require minimal support removal, additional steps like bead blasting or dyeing might be necessary to achieve certain aesthetic or functional qualities.
The Future of MJF Printing
The future of MJF looks promising, with ongoing advancements aimed at enhancing material capabilities, increasing throughput, and further improving part quality. As the technology matures, it’s expected to become more accessible, potentially expanding into new markets and applications.
Multi Jet Fusion represents a significant advancement in the field of 3D printing, offering a powerful combination of speed, precision, and strength. Its ability to rapidly produce parts that meet stringent quality standards makes MJF an invaluable tool in modern manufacturing. For industries that prioritize efficiency and part performance, MJF presents a compelling option, promising not only to streamline production processes but also to innovate them.