Fused Deposition Modeling (FDM), also known as Fused Filament Fabrication (FFF), stands out as one of the most commonly adopted 3D printing technologies in both amateur and professional spheres. Recognized for its efficiency and affordability, FDM has become a staple in various sectors, providing an accessible entry point into the world of additive manufacturing.
How FDM Printing Works
FDM operates on a fairly straightforward principle: thermoplastic material is heated to a semi-liquid state and extruded through a nozzle, layer by layer, to build an object. The process begins with the design of a 3D model using CAD software, which is then translated into a format suitable for printing. Special slicing software converts the model into instructions for the printer, determining how each layer will be laid.
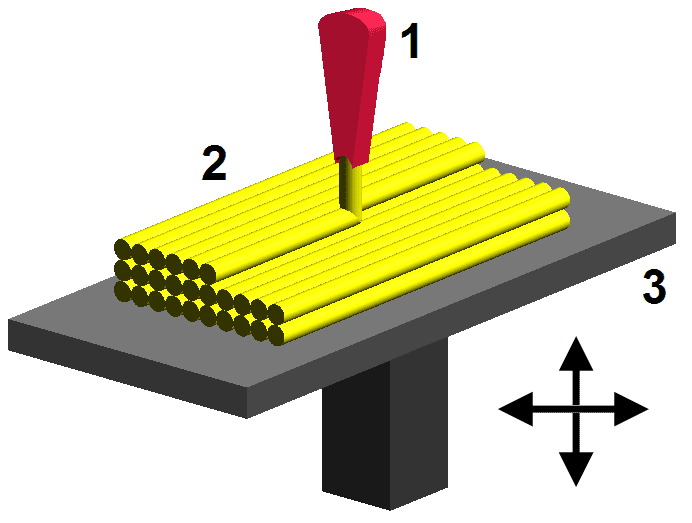
During printing, the filament is fed through a heated extruder, melting it just enough to allow it to be shaped as it is laid down. The extruder moves over the build platform in a predetermined path, depositing the material, which cools and solidifies quickly, bonding with the layer beneath it. This layer-by-layer deposition continues until the entire object is formed from the ground up.
Advantages of FDM 3D Printing
FDM technology offers several compelling benefits that make it a popular choice:
Cost-Effectiveness: FDM printers are generally less expensive than other types of 3D printers, making them ideal for hobbyists and small businesses. The materials used in FDM, primarily standard thermoplastics like ABS and PLA, are also widely available and affordable.
Material Durability: Parts produced by FDM are typically robust and functional, capable of withstanding significant stress depending on the plastic used. This makes FDM ideal for creating mechanical parts, prototypes, and items that require higher structural integrity.
Applications of FDM 3D Printing
The practical applications of FDM are diverse and extend across various fields:
Prototyping: Rapid prototyping with FDM allows designers and engineers to iterate quickly and cost-effectively.
Education: Schools and universities utilize FDM for teaching engineering and design principles, thanks to its safety and ease of use.
Manufacturing: From custom tooling and fixtures to end-use products, FDM can be found in manufacturing environments, especially for low-volume production or custom parts.
Personal Use: The DIY community embraces FDM for its versatility in creating custom household items, toys, and decorations.
Considerations and Limitations
While FDM is versatile, it has its limitations:
Surface Finish: The layer-by-layer process can leave visible lines on the surface of the print, which might require post-processing like sanding or chemical smoothing for aesthetic purposes.
Strength Variances: The strength of FDM parts can vary with orientation due to the layering process. Parts are generally weaker along the Z-axis, where layer bonding occurs.
Material Limitations: While many thermoplastics are available, each has its characteristics and limitations, such as susceptibility to warping or moisture absorption.
The Future of FDM Printing
Advancements in FDM technology continue to enhance its capabilities. Innovations in extruder design, higher precision control systems, and the development of new materials with improved properties are broadening the applications of FDM. The focus is on achieving higher quality finishes, increased strength, and faster production times.
Fused Deposition Modeling (FDM) remains a cornerstone of 3D printing technologies due to its straightforward methodology, cost efficiency, and the robustness of its products. As the technology evolves, it is expected to open up even more possibilities for both professional and personal use. Whether you are a designer, engineer, educator, or hobbyist, FDM offers a practical gateway into the expansive world of 3D printing.