Materials engineering, a field crucial for developing new materials and improving existing ones, has been significantly transformed by the advent of 3D printing technology. Known for its ability to layer materials into precise, complex structures, 3D printing has opened new frontiers in the design and testing of materials. This technology enables researchers and engineers to explore novel material composites and configurations, accelerating advancements in various industries including aerospace, automotive, and biomedical.
The Impact of 3D Printing on Materials Engineering
3D printing, or additive manufacturing, has revolutionized materials engineering by allowing for the direct fabrication of complex geometries that were previously difficult or impossible to achieve. This capability not only enhances the functional properties of materials but also optimizes their mechanical, thermal, and electrical performance. As a result, 3D printing is not just a manufacturing technique but also a tool for material innovation.
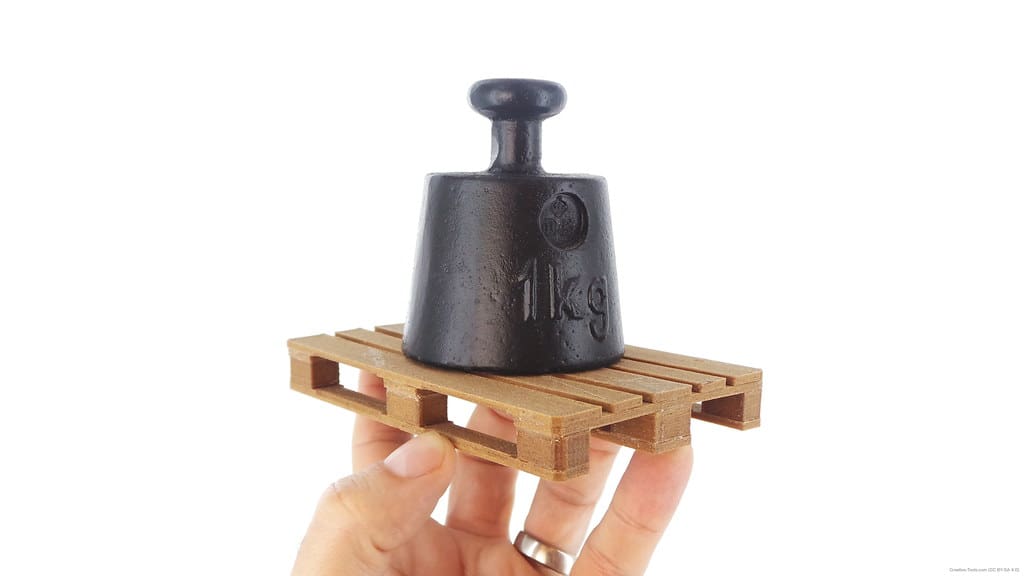
Advantages of 3D Printing in Materials Engineering
Customization and Complexity: 3D printing excels in producing bespoke items with complex internal structures, such as lightweight lattice frameworks for aerospace applications or porous scaffolds for biomedical implants. These structures can be optimized for specific functions, enhancing performance while reducing material usage.
Rapid Prototyping and Testing: Materials engineering often involves iterative testing and refinement. 3D printing accelerates this process by allowing quick production of prototypes directly from digital models. This rapid prototyping capability enables more extensive testing and faster optimization of material properties.
Material Diversity and Hybridization: One of the significant advantages of 3D printing is its ability to handle multiple materials in a single print. Engineers can create graded or hybrid materials that transition between different properties, opening up new possibilities for material science.
Waste Reduction: Traditional manufacturing processes, such as machining and casting, typically produce a significant amount of waste. In contrast, 3D printing adds material layer by layer, significantly reducing waste and often using less material overall.
Key Applications of 3D Printing in Materials Engineering
Aerospace and Automotive Components: In aerospace and automotive sectors, the demand for high-performance, lightweight materials is constant. 3D printing allows for the design of parts with complex geometries that are lighter yet still robust, contributing to overall efficiency improvements in vehicles and aircraft.
Biomedical Implants and Devices: The biomedical field has benefited immensely from 3D printing in materials engineering. Custom implants, prosthetics, and surgical tools designed to match the specific anatomical features of individual patients are now possible, improving clinical outcomes and patient comfort.
Energy Storage and Electronics: 3D printing is used to develop advanced energy storage systems, including batteries and supercapacitors with highly efficient and compact designs. Additionally, it allows for the fabrication of electronic devices with novel architectures, such as flexible electronics and integrated sensors.
Protective Gear and Equipment: Customized protective gear, such as helmets and body armor, can be 3D printed to match the precise size and preferences of the user, providing better protection and comfort. These items can be engineered with advanced material composites to enhance their protective properties.

Challenges in 3D Printing for Materials Engineering
Despite its many advantages, 3D printing faces several challenges in materials engineering:
Material Properties: Ensuring that 3D printed materials meet the necessary mechanical and thermal properties for specific applications remains a challenge, especially when compared to traditionally manufactured materials.
Scalability: While 3D printing is excellent for prototypes and small-scale production, scaling it for large-volume manufacturing can be economically and technically challenging.
Quality Control and Standardization: Achieving consistent quality and meeting stringent industry standards can be difficult with 3D printing, as the properties of 3D printed materials can vary depending on the machine, material batch, and process parameters.
Future Directions in 3D Printing for Materials Engineering
The future of 3D printing in materials engineering looks promising with ongoing advancements in printer technology and material science. Innovations such as faster printing speeds, larger build volumes, and improved material properties are expected. Furthermore, as the technology matures, it is likely to become more integrated into traditional manufacturing processes, complementing rather than replacing conventional methods.
Researchers are also exploring the potential of 4D printing, where 3D printed objects can change shape or properties in response to external stimuli, such as temperature or humidity. This development could open up new applications in adaptive materials and smart structures.
3D printing is poised to continue its transformative impact on materials engineering, driving innovations that improve product performance, reduce costs, and lead to more sustainable manufacturing practices. As the technology continues to evolve, it offers exciting possibilities for developing new materials and revolutionizing traditional industries. For materials engineers, embracing 3D printing is not just about adopting new technology—it’s about leading the way in the future of manufacturing.