Instrumentation engineering focuses on the design, development, and maintenance of systems used to measure, control, and monitor processes within various industries. This discipline is crucial for ensuring accuracy, efficiency, and safety in processes ranging from manufacturing to energy production and beyond. 3D printing, also known as additive manufacturing, has significantly impacted instrumentation engineering by offering innovative ways to create complex components and tailor-made solutions rapidly and cost-effectively.
The Emergence of 3D Printing in Instrumentation Engineering
3D printing has transcended its initial use as a tool for rapid prototyping to become a fundamental part of the production process in instrumentation engineering. The technology’s ability to produce intricate and precise components quickly aligns perfectly with the needs of instrumentation engineering, where custom-fit and functionality are paramount. As 3D printing technologies have advanced, they have enabled the direct manufacturing of instruments and parts that meet specific engineering requirements.
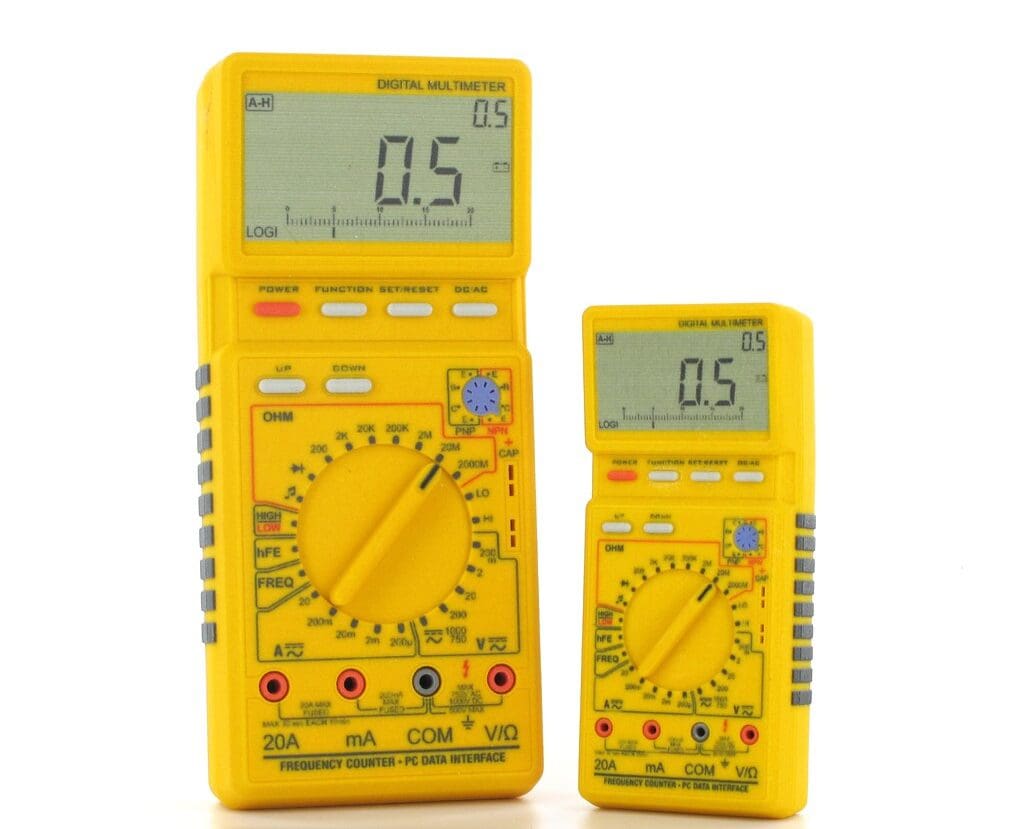
Advantages of 3D Printing in Instrumentation Engineering
Customization and Precision: 3D printing allows for the design and creation of highly specialized instrumentation components tailored to precise specifications. This level of customization is vital for applications where standard solutions are inadequate.
Complexity Without Compromise: Additive manufacturing excels in producing complex geometries that are often impossible or too costly to achieve with traditional manufacturing methods. For instrumentation engineering, this means the ability to integrate complex internal channels, lightweight structures, or multifunctional components seamlessly.
Speed of Development: The rapid prototyping capabilities of 3D printing enable engineers to iterate designs quickly, test prototypes, and refine functionality without the lengthy lead times associated with conventional fabrication methods.
Cost Efficiency: Reducing the need for expensive molds and assemblies, 3D printing lowers the cost barrier for developing bespoke instrumentation solutions, particularly for low-volume or highly specialized applications.
Key Applications of 3D Printing in Instrumentation Engineering
Sensor Housings and Enclosures: Custom-designed housings that protect sensitive instrumentation from environmental conditions can be efficiently produced with 3D printing, ensuring that sensors operate reliably under any circumstances.
Fluid Handling Components: The precise control of fluid dynamics is crucial in many instruments, especially in fields like biomedical or chemical engineering. 3D printing can create complex fluidic pathways and components that optimize the flow and mixing of liquids or gases.
Custom Tooling for Instrument Assembly: Specialized tools required for assembling intricate instruments can be designed and printed directly, facilitating the manufacturing process and ensuring high-quality construction.
Prototype Development of Measurement Devices: Whether for pressure gauges, thermocouples, or accelerometers, 3D printing allows for the rapid development and testing of new measurement devices, speeding up innovation and implementation.

Challenges in 3D Printing for Instrumentation Engineering
Material Limitations: The range of materials suitable for 3D printing still has limitations, particularly concerning durability, chemical resistance, and thermal stability, which are often required for instrumentation components.
Precision and Repeatability: Achieving the high precision required for instrumentation components consistently can be challenging with 3D printing, especially when dealing with very small scales or tight tolerances.
Integration with Traditional Manufacturing: While 3D printing offers significant advantages, integrating these parts with components made through traditional manufacturing processes can be challenging, requiring careful design and compatibility considerations.
Regulatory and Standards Compliance: Instrumentation often needs to meet strict regulatory standards, particularly in industries like healthcare and aerospace. Ensuring that 3D printed components comply with these standards can require extensive testing and validation.
Future Directions in 3D Printing for Instrumentation Engineering
The future of 3D printing in instrumentation engineering is promising, with ongoing advancements in materials science, printing technologies, and digital design tools. Innovations are likely to focus on improving the precision, strength, and functional properties of printed components. Furthermore, the development of new composite materials and the integration of electronics directly into printed parts are expected to enhance the functionality and range of applications for 3D printed instrumentation.
3D printing is transforming instrumentation engineering by enabling more rapid, flexible, and cost-effective development of specialized instruments and components. As the technology continues to evolve, it promises to unlock further potential in the design and manufacturing of precise and customized instrumentation, contributing to advancements across a wide range of industrial sectors. With ongoing innovations, 3D printing will increasingly become a crucial technology in the field of instrumentation engineering, reshaping how engineers approach the challenges of measurement, control, and monitoring.