Helicopter manufacturing, characterized by complex engineering challenges and stringent safety requirements, is increasingly benefiting from the advent of 3D printing technology. This innovative manufacturing approach, also known as additive manufacturing, enables the production of lightweight, complex components that are often impossible to create using traditional methods. As the aviation industry continues to seek advancements in performance, safety, and cost-efficiency, 3D printing emerges as a transformative tool, offering significant improvements across various aspects of helicopter design and production.
The Emergence of 3D Printing in Helicopter Manufacturing
Initially used for rapid prototyping, 3D printing has evolved to facilitate the production of functional, structural components in helicopters. This shift is driven by advancements in 3D printing technologies and materials capable of meeting the aerospace industry’s rigorous standards. Manufacturers now utilize 3D printing not only to reduce the weight and increase the performance of helicopters but also to streamline production processes, reduce costs, and decrease lead times.
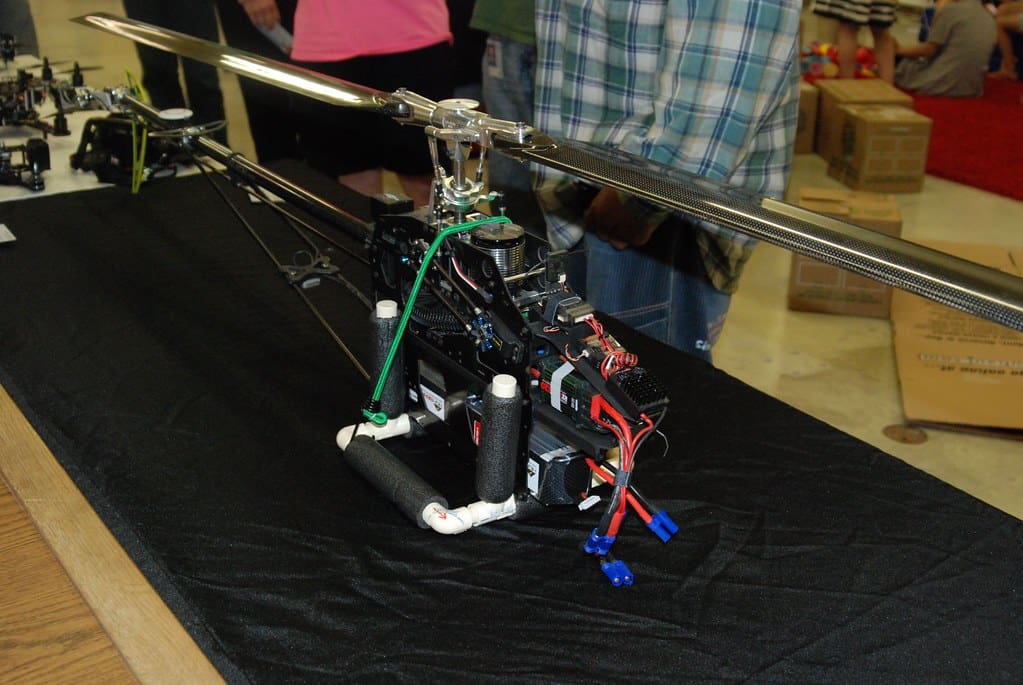
Advantages of 3D Printing in Helicopters
Complex Geometries and Lightweight Structures: 3D printing excels at creating intricate designs that enhance the functionality and reduce the weight of components. Lightweight structures are particularly beneficial in helicopter manufacturing, where weight reduction directly impacts fuel efficiency and flight capabilities.
Customization and Flexibility: 3D printing allows for high levels of customization without significant cost increases. This is crucial in manufacturing specialized helicopter parts and in customizing interiors to meet specific operational roles, whether in medical evacuation, search and rescue, or luxury transport.
Reduced Material Waste: Unlike traditional subtractive manufacturing methods, 3D printing adds material layer by layer to create a part, significantly reducing waste. This efficiency is not only cost-effective but also aligns with the industry’s growing environmental sustainability goals.
Improved Supply Chain Efficiency: With 3D printing, helicopter manufacturers can produce parts on demand, simplifying logistics and inventory management. This capability is especially valuable for maintaining and repairing older helicopters where parts may no longer be readily available.
Key Applications of 3D Printing in Helicopters
Rotor Blades and Components: Advanced composite materials and 3D printing techniques are used to produce rotor blades and associated mechanisms. These components can be optimized for aerodynamic efficiency and durability, enhancing the helicopter’s performance and safety.
Engine Parts: Lightweight and heat-resistant engine components, such as fuel nozzles and turbine blades, are produced using 3D printing. These parts often feature complex designs that are optimized for improved airflow and thermal management.
Custom Interiors: 3D printing enables the creation of ergonomic and lightweight interior components tailored to specific missions or customer preferences. This includes seats, instrument panel enclosures, and cabin fixtures, which can be designed to maximize comfort and functionality.
Prototyping and Testing: Rapid prototyping of new helicopter designs and components accelerates development cycles, allowing for quicker iteration based on testing and feedback. This rapid prototyping is crucial for developing innovative solutions that meet unique operational requirements.
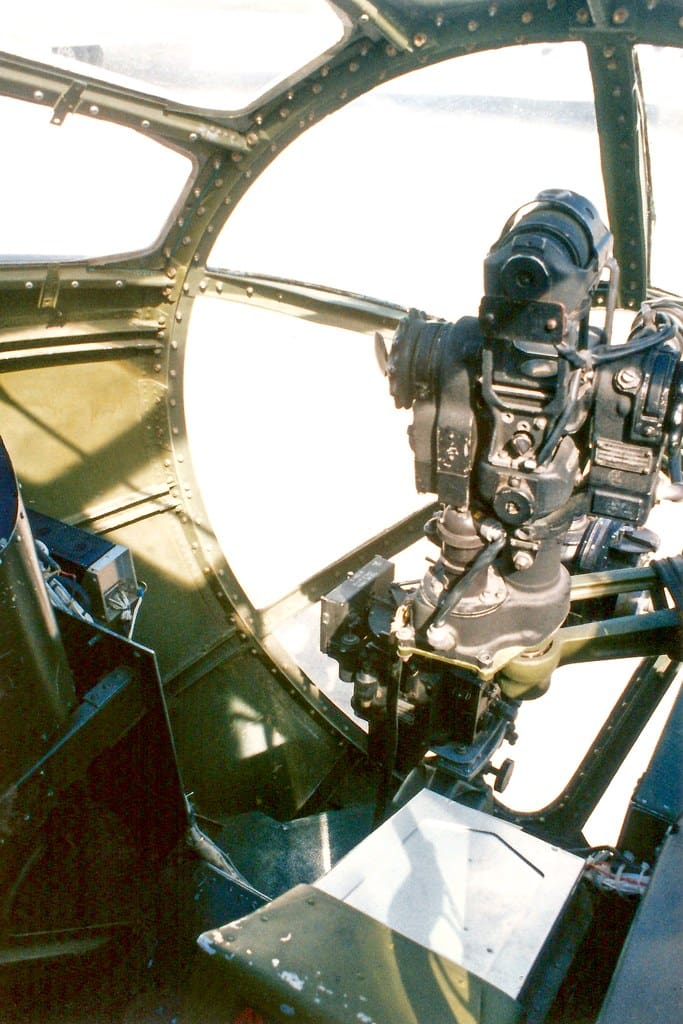
Challenges in 3D Printing for Helicopters
Despite its advantages, there are several challenges associated with the use of 3D printing in helicopter manufacturing:
Material Performance: Ensuring that 3D-printed materials meet the necessary standards for strength, durability, and resistance to environmental factors is crucial. The development of new materials that can satisfy these stringent requirements is ongoing.
Certification Processes: Obtaining certification for 3D-printed helicopter parts involves rigorous testing and validation to meet aviation standards. This process can be lengthy and complex, particularly for structural components critical to flight safety.
Scaling Production: While 3D printing is ideal for low-volume production and prototyping, scaling up to higher production volumes required by commercial and military applications remains a challenge.
Future Directions in 3D Printing for Helicopters
The future of 3D printing in helicopter manufacturing is promising, with ongoing advancements in printer technology, materials science, and digital design tools expected to mitigate current limitations. Innovations such as multi-material printing and the integration of artificial intelligence in design processes could further enhance the capabilities and applications of 3D printing, leading to more widespread adoption in the industry.
3D printing is set to continue its transformative impact on helicopter manufacturing, offering new levels of efficiency, customization, and innovation. As the technology evolves, it promises to reshape the landscape of rotorcraft engineering, enabling the production of more advanced, reliable, and cost-effective helicopters. This revolution in manufacturing technology not only benefits the aviation industry but also enhances the capabilities of helicopters to perform critical missions around the world.