Electrical engineering, a discipline that significantly shapes our interactions with technology, is undergoing a transformative shift with the adoption of 3D printing. This innovative manufacturing process, known as additive manufacturing, is enhancing the way electrical components, systems, and circuits are designed, prototyped, and produced. From consumer electronics to complex electrical systems, 3D printing offers unprecedented flexibility and efficiency, driving advancements in design complexity, customization, and integration of electrical components.
The Emergence of 3D Printing in Electrical Engineering
3D printing first gained traction in industries requiring high precision and customization, such as aerospace and medical devices. Its application in electrical engineering has expanded these benefits to the production of complex electronic components and systems. Engineers now use 3D printing to create conductive paths, integrate electronic functionality into unique substrates, and develop devices with embedded electronics, which were previously unimaginable due to traditional manufacturing constraints.
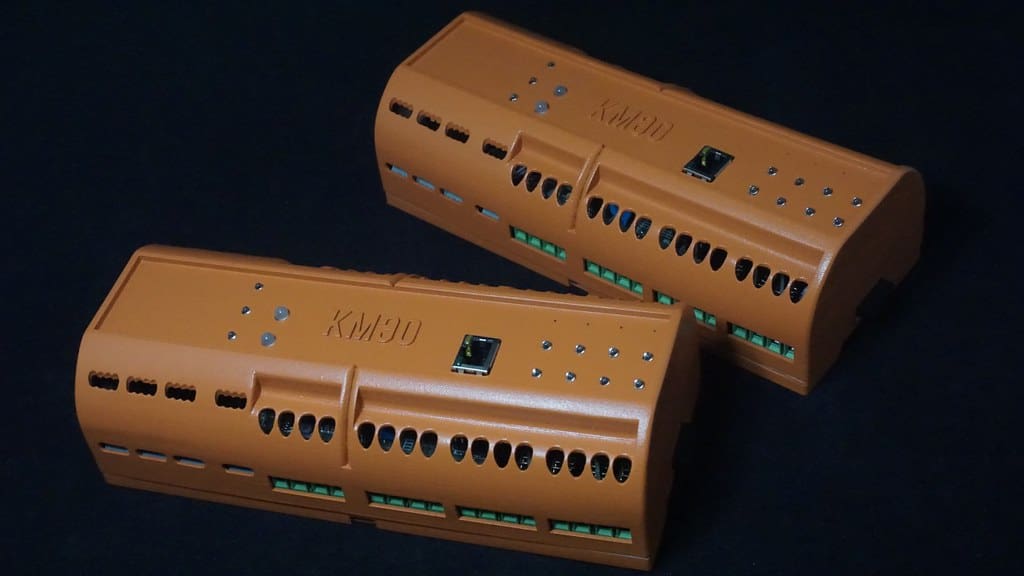
Advantages of 3D Printing in Electrical Engineering
Rapid Prototyping: 3D printing accelerates the development cycle of electrical components and devices. Engineers can quickly move from design to prototype, allowing for faster iteration and optimization of electronic products.
Complexity and Miniaturization: With 3D printing, electrical components can be produced with intricate, detailed structures at a micro-scale. This capability is crucial for the advancement of miniaturized electronics and for applications where space and weight are limiting factors, such as in mobile devices and drones.
Customization and Flexibility: 3D printing allows for the customization of electronics to specific needs without significant cost increases. This adaptability is particularly beneficial for specialized or low-volume production runs, such as bespoke sensors or tailored connectivity solutions for smart devices.
Integration of Multiple Functions: Advanced 3D printing techniques enable the integration of multiple electrical functions into a single process, reducing assembly steps and improving performance. For example, a complete sensor array with embedded wiring can be produced in one print cycle, enhancing reliability and efficiency.
Key Applications of 3D Printing in Electrical Engineering
Printed Circuit Boards (PCBs): 3D printing is revolutionizing the production of PCBs by enabling the direct printing of conductive, insulating, and substrate materials in a single process. This method allows for greater design freedom, the production of more compact boards, and the integration of PCBs into unconventional shapes and spaces.
Antennas and RF Components: The fabrication of antennas and RF components using 3D printing allows for complex designs that improve signal performance and device integration. This is particularly valuable in telecommunications and consumer electronics, where device miniaturization continues to be a strong trend.
Sensors and Actuators: 3D printing enables the creation of sensors and actuators with complex geometries and multi-material designs. These components are essential in various applications, including robotics, automotive systems, and medical devices, where tailored functionality and form factors are crucial.
Wearable Electronics: In the growing field of wearable technology, 3D printing is used to integrate electronic components directly into wearable formats, such as fabrics or flexible materials. This integration is essential for developing seamless, comfortable smart garments and accessories.

Challenges in 3D Printing for Electrical Engineering
Despite its benefits, several challenges limit the widespread adoption of 3D printing in electrical engineering:
Material Limitations: The range of conductive and high-performance electronic materials suitable for 3D printing is still limited. Developing materials that meet the conductivity, reliability, and durability standards for electronic components is ongoing.
Precision and Reliability: Achieving the high levels of precision and reliability required for electronic components through 3D printing can be challenging. Ensuring consistent quality and performance in printed electronics is critical, especially for safety-critical applications.
Scaling Production: While 3D printing is excellent for prototyping and small production runs, scaling up to mass production remains cost-prohibitive and technically challenging compared to traditional manufacturing methods.
Future Directions in 3D Printing for Electrical Engineering
The future of 3D printing in electrical engineering looks promising, with ongoing research focused on improving material properties, printing techniques, and integration processes. Innovations in multi-material printing and the development of new conductive materials are expected to address current limitations and open up new applications in electronics manufacturing.
3D printing is set to significantly impact electrical engineering by providing enhanced capabilities for designing and manufacturing advanced electronic components. As the technology continues to evolve, it promises to drive innovations across various sectors, leading to smarter, more integrated, and highly customizable electronic solutions. Embracing 3D printing in electrical engineering not only streamlines production processes but also fosters creativity and technological advancement in the field.