The drone industry is rapidly evolving, fueled by advances in technology that continually enhance the capabilities and applications of unmanned aerial vehicles (UAVs). Among these technologies, 3D printing has emerged as a game-changer, offering unprecedented flexibility and efficiency in drone design and manufacturing. From consumer drones to commercial and military applications, 3D printing is revolutionizing how drones are conceived, produced, and deployed, enabling customized solutions and driving innovation in the field.
The Emergence of 3D Printing in Drone Manufacturing
Initially used for prototyping across various industries, 3D printing has quickly transitioned to the production of end-use components, particularly in the dynamic world of drone technology. This shift is driven by the ability of 3D printing to produce lightweight, complex structures that are ideal for the unique requirements of drone operations. Today, 3D printing is not just reshaping the design and production processes but also enhancing the performance and functionality of drones through innovative uses of materials and design techniques.
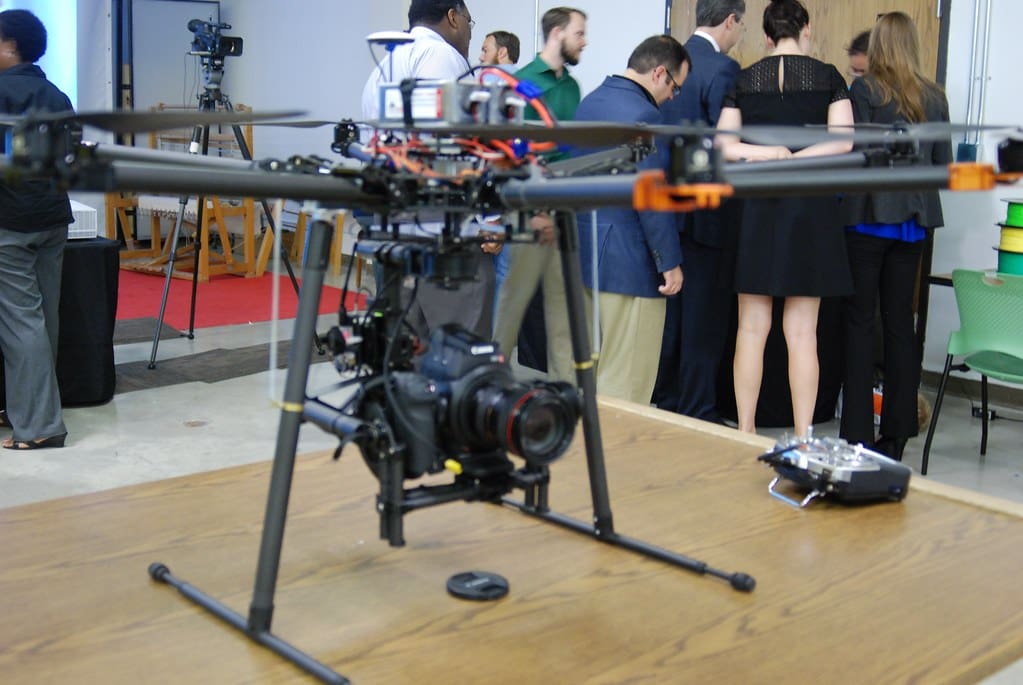
Advantages of 3D Printing in Drones
Design Flexibility and Complexity: 3D printing allows for the creation of complex geometries that are often impossible with traditional manufacturing methods. This capability is crucial for drones, where the integration of aerodynamic features and lightweight structures can significantly impact performance.
Rapid Development and Customization: The technology enables rapid prototyping and iterative design, allowing engineers to quickly test and refine their drone designs. Moreover, 3D printing facilitates customization of drones for specific applications, such as agricultural monitoring, search and rescue operations, or aerial photography.
Weight Reduction: One of the most significant benefits of 3D printing is its ability to produce lightweight components. Lighter drones can fly longer and carry more payload, which is especially important for commercial and military applications.
Cost-Effectiveness: By reducing material waste and eliminating the need for expensive molds and tooling, 3D printing can lower production costs. This is particularly beneficial for small-scale manufacturers and hobbyists who need cost-effective solutions to develop and market their drones.
Key Applications of 3D Printing in Drones
Airframe Components: Many drones feature airframes that are entirely or partially manufactured using 3D printing. These components benefit from being lightweight yet strong, with integrated features that simplify assembly and maintenance.
Propellers and Ducts: 3D printing is used to produce optimized propellers and ducts that enhance aerodynamic efficiency and reduce noise. These components can be tailored to specific flight characteristics or environmental conditions.
Custom Payloads and Attachments: From camera mounts to sensor housings, 3D printing enables the development of customized payloads that fit specific missions or equipment, allowing drone operators to expand their capabilities.
Replacement Parts: The ability to quickly print replacement parts on-demand is a significant advantage, particularly for drone operators in remote locations. This not only minimizes downtime but also extends the operational life of the drone.

Challenges in 3D Printing for Drones
Despite its potential, the integration of 3D printing in drone manufacturing faces several challenges:
Material Durability and Performance: Ensuring that 3D-printed materials can withstand the stresses of flight and environmental conditions is crucial. Materials need to be robust, resistant to impact, and stable over a range of temperatures and weather conditions.
Scaling Production: While 3D printing is excellent for prototyping and small production runs, scaling up to mass production can be challenging. The speed of printing and the cost of materials can be prohibitive for large-scale manufacturing.
Regulatory and Safety Standards: Drones must meet specific safety and regulatory standards, particularly in commercial and military applications. Certifying 3D-printed drone components for compliance with these standards can be a complex and lengthy process.
Future Directions in 3D Printing for Drones
The future of 3D printing in drones looks promising, with ongoing advancements in printer technologies, materials science, and digital design expected to address current limitations. Innovations such as multi-material printing and the integration of electronic components during the printing process could further enhance the capabilities and applications of drones.
3D printing is set to continue its transformative impact on the drone industry, providing new levels of flexibility, efficiency, and innovation. As the technology evolves, it promises to enable more sophisticated, application-specific drone designs that could revolutionize fields ranging from environmental monitoring and disaster relief to defense and entertainment. This technological convergence is not just enhancing the operational capabilities of drones but also reshaping the landscapes they operate in.