Computer Aided Design (CAD) is a critical tool in the engineering, architecture, and product development fields, facilitating the creation, modification, analysis, and optimization of designs. The integration of 3D printing into CAD processes has revolutionized how professionals visualize and realize their conceptual designs. This transformative technology enables the direct physical manifestation of CAD models, offering a tangible and interactive perspective that enhances understanding, communication, and testing of designs before mass production.
The Emergence of 3D Printing in CAD
Initially used primarily for prototyping, 3D printing has expanded its capabilities to include the production of end-use products across various industries. This evolution is driven by advancements in 3D printing technologies and materials that meet diverse and demanding application requirements. Today, 3D printing is not merely a tool for creating prototypes but a vital component of the design process, seamlessly integrated into CAD software through plugins and direct export options, facilitating a streamlined transition from digital model to physical part.
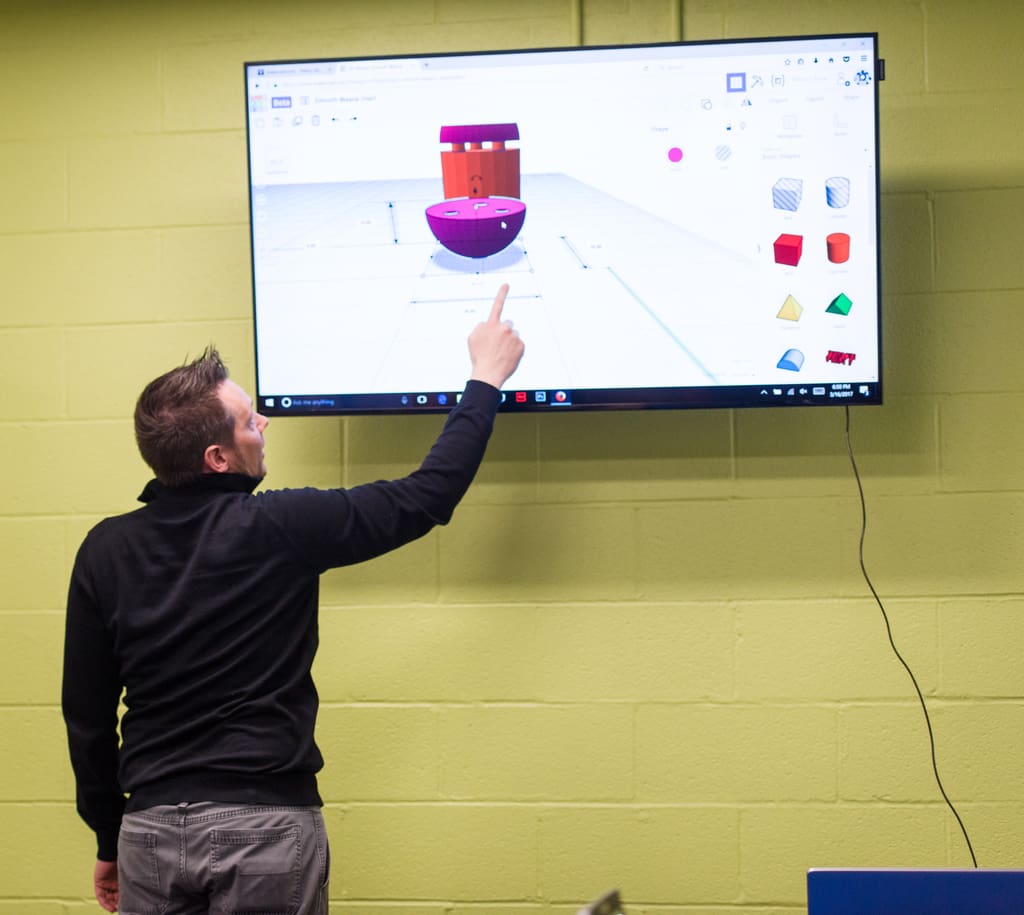
Advantages of 3D Printing in CAD
Enhanced Visualization and Prototyping: 3D printing allows designers and engineers to quickly convert their digital models into physical objects. This capability is invaluable for troubleshooting, demonstrating, and refining designs, providing a clear and immediate understanding of the feasibility and functionality of a design.
Iterative Design and Rapid Testing: The speed and efficiency of 3D printing enable rapid iteration of designs. Designers can test ideas, make modifications, and reimplement them in a cycle that drastically shortens development times and enhances the final product’s quality.
Customization and Complexity: 3D printing excels in producing complex geometries that are often impossible to fabricate through traditional manufacturing methods. CAD software can be used to design intricate and tailored items that 3D printers can produce without the need for specific tooling or molds.
Cost Reduction: For small production runs and custom parts, 3D printing can be more cost-effective than traditional manufacturing methods. By reducing the need for expensive molds and cutting down on material waste, 3D printing minimizes overall production costs.
Key Applications of 3D Printing in CAD
Product Development: From consumer electronics to furniture design, 3D printing allows product developers to create prototypes that accurately reflect the intended design, function, and aesthetics of their products, enabling more effective testing and product validation.
Architecture and Construction: Architects use 3D printing to create detailed models of buildings and structures, allowing for better visualization of the finished project and the potential to test different construction materials and methods.
Automotive and Aerospace: In industries where customization and performance optimization are crucial, 3D printing enables engineers to produce parts that are lighter, stronger, and more complex than those made through conventional manufacturing.
Medical and Dental: CAD combined with 3D printing is particularly transformative in medical and dental fields, where personalized implants, prosthetics, and surgical aids can be designed and produced to fit the unique anatomy of individual patients.
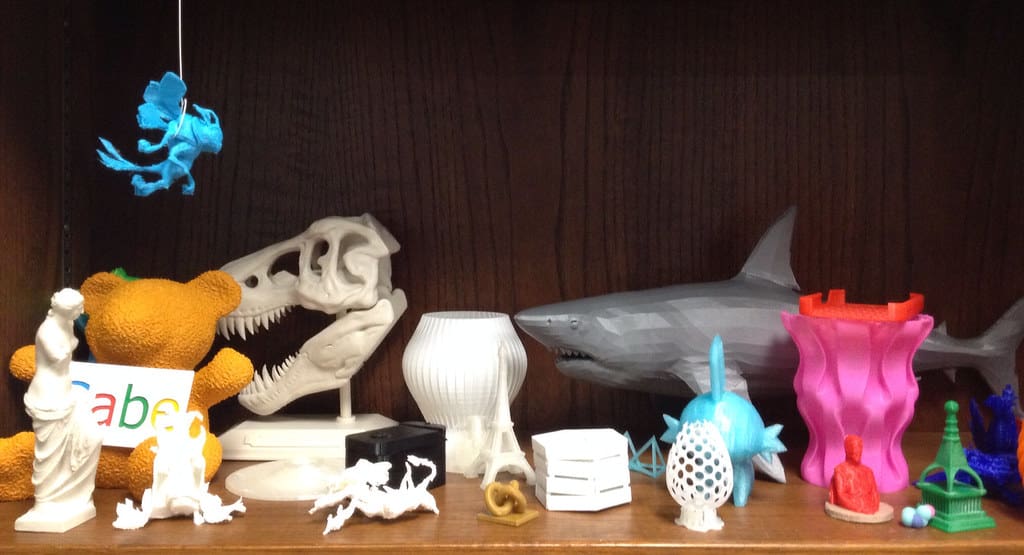
Challenges in 3D Printing for CAD
Despite its many advantages, several challenges remain in fully integrating 3D printing into CAD workflows:
Material Limitations: The range of materials suitable for 3D printing is continuously expanding, yet it still does not match the diversity available through traditional manufacturing methods. Material properties such as strength, flexibility, and temperature resistance can limit the application of 3D printed parts.
Surface Finish and Precision: While 3D printing technologies are continually improving, achieving the surface finish and precision required for some industrial applications can still be challenging without post-processing steps.
Scalability: Although 3D printing is excellent for prototyping and small production runs, scaling to large volumes can be impractical due to speed and cost constraints compared to traditional manufacturing methods.
Technical Skills and Integration: Fully integrating 3D printing into CAD requires a deep understanding of both the design software and the specific capabilities and limitations of 3D printing technologies. This often necessitates additional training and expertise.
Future Directions in 3D Printing for CAD
The future of 3D printing in CAD is promising, with ongoing advancements likely to address current limitations and expand its capabilities. Innovations in printer technologies, development of new materials, and tighter integration with CAD software are expected to enhance the precision, efficiency, and usability of 3D printing for professional design and manufacturing.
3D printing has become an indispensable tool in CAD, providing significant advantages in terms of visualization, prototyping, and production. As the technology continues to evolve, it will further transform the design landscape, enabling more rapid, cost-effective, and innovative development across various industries.