In the innovative landscape of chemical engineering, 3D printing is emerging as a transformative technology that is reshaping traditional methodologies and enhancing the capabilities of chemical processes. This technology, also known as additive manufacturing, offers unparalleled precision, efficiency, and customization, making it an invaluable tool in the development and production of chemical products.
The Emergence of 3D Printing in Chemical Engineering
3D printing has been steadily gaining traction across various engineering disciplines, but its application in chemical engineering is particularly revolutionary. Initially utilized for creating prototypes and models, 3D printing has evolved to facilitate complex chemical production processes, including the fabrication of reactors, fluidic devices, and other chemical processing equipment. The ability to design and produce equipment with complex internal geometries that are otherwise difficult to manufacture opens up new possibilities for process optimization and innovation.
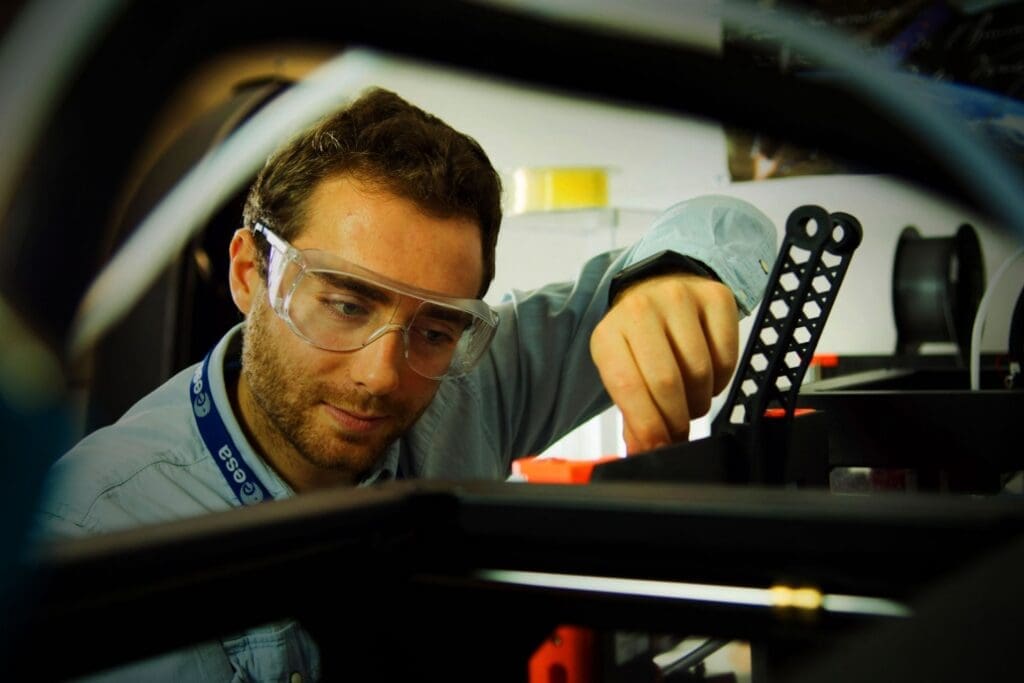
Advantages of 3D Printing in Chemical Engineering
Complex Geometries and Microscale Precision: One of the most significant advantages of 3D printing in chemical engineering is the ability to create complex internal structures. These structures can significantly enhance the efficiency of chemical reactions by optimizing mass transfer and heat exchange.
Rapid Prototyping and Iterative Design: 3D printing allows for rapid prototyping, enabling engineers to quickly test and refine their designs. This agility is crucial in research and development, where multiple iterations of a design are common before achieving the desired outcome.
Customization and Scalability: With 3D printing, chemical engineers can produce bespoke solutions tailored to specific processes or production needs. Moreover, 3D printing offers scalability from small laboratory setups to larger production scales, providing flexibility in manufacturing and research.
Cost Reduction and Material Efficiency: Traditional manufacturing of chemical process equipment can be costly and material-intensive. 3D printing reduces these costs by minimizing waste through additive processes and lowering the expense associated with custom tooling and setup.
Key Applications of 3D Printing in Chemical Engineering
Catalyst Design and Production: Catalysts are crucial in increasing the efficiency of chemical reactions. 3D printing allows for the precise fabrication of catalyst structures with optimized surface areas and porosities, enhancing reaction rates and selectivity.
Chemical Reactors and Mixing Devices: Engineers can use 3D printing to develop reactors and mixers with complex geometries designed for specific reactions. These devices can achieve more efficient mixing and improved thermal management, leading to better reaction outcomes and energy savings.
Microfluidic Devices: In chemical analysis and small-scale reactions, microfluidic devices play a pivotal role. 3D printing enables the production of these devices with precise channels and compartments, facilitating the controlled movement and mixing of small volumes of fluids.
Separation Units: 3D printing can be used to create tailored components for separation processes, such as membranes or adsorptive units. These components can be designed to maximize the surface area and optimize flow paths, enhancing the efficiency of separation processes.
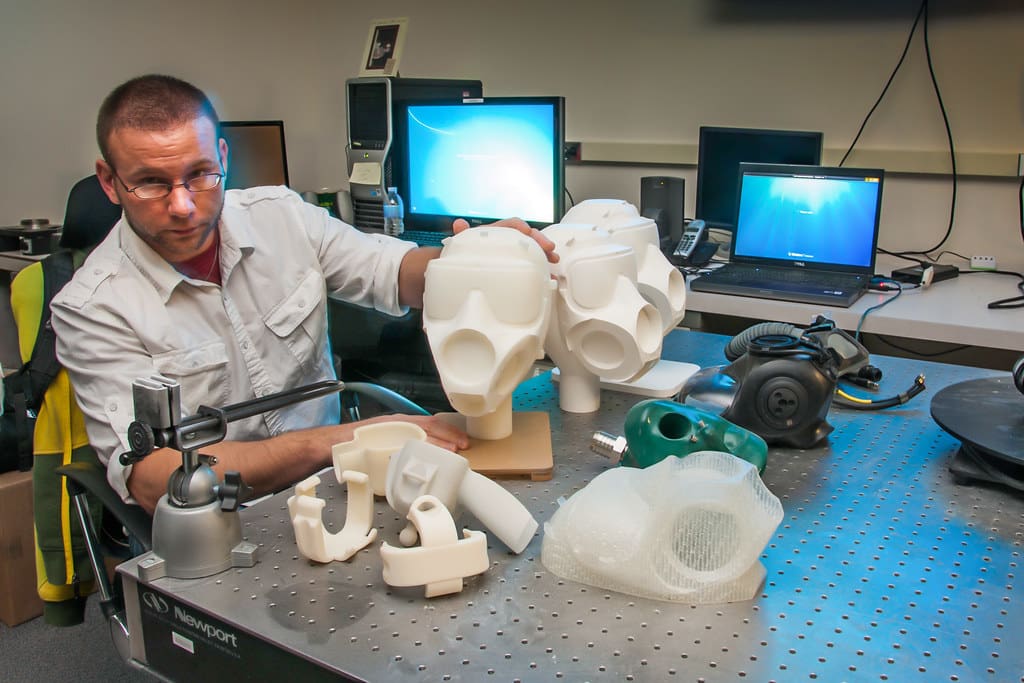
Challenges in 3D Printing for Chemical Engineering
Despite its benefits, 3D printing faces several challenges in its application in chemical engineering:
Material Compatibility: The chemicals used in various processes may be corrosive or reactive, requiring materials that can withstand harsh conditions. Finding suitable materials for 3D printing that meet these chemical resistance requirements remains a challenge.
Regulatory and Safety Concerns: Chemical engineering often involves processes that are subject to strict regulatory standards. Ensuring that 3D-printed components comply with these standards, particularly in terms of safety and environmental impact, is essential.
Scalability and Integration: While 3D printing offers scalability, transitioning from small-scale production to industrial-scale processes can be challenging. Integrating 3D-printed components into existing chemical plants requires careful consideration of process dynamics and compatibility.
Future Directions in 3D Printing for Chemical Engineering
The future of 3D printing in chemical engineering is promising, with ongoing research and development poised to address current limitations and expand its applications. Innovations in printable materials that can resist extreme temperatures and corrosive environments are expected. Additionally, the integration of 3D printing with digital and automation technologies could lead to smarter, more efficient chemical manufacturing processes.
3D printing is set to revolutionize chemical engineering by providing tools to design more efficient, cost-effective, and tailored equipment and processes. As the technology advances, it holds the potential to significantly impact the chemical industry, driving innovation and sustainability. Embracing 3D printing in chemical engineering not only enhances current practices but also paves the way for future advancements in the field.