3D printing, also known as additive manufacturing, has transcended its initial applications to become a fundamental part of material technology. This evolving field continually introduces new materials that expand the capabilities and applications of 3D printing across various industries, from aerospace to biomedicine. Innovations in material technology not only enhance the properties and performance of 3D printed objects but also drive sustainability and efficiency in manufacturing processes.
The Emergence of 3D Printing in Material Technology
The integration of new materials into 3D printing technology has significantly broadened the scope of what can be achieved through additive manufacturing. Early 3D printers were limited to a few plastics and resin-based materials, but today’s printers can handle a diverse range of substances, including metals, ceramics, and composites. Each advancement in material technology not only opens up new industrial applications but also improves the precision, durability, and functionality of printed products.
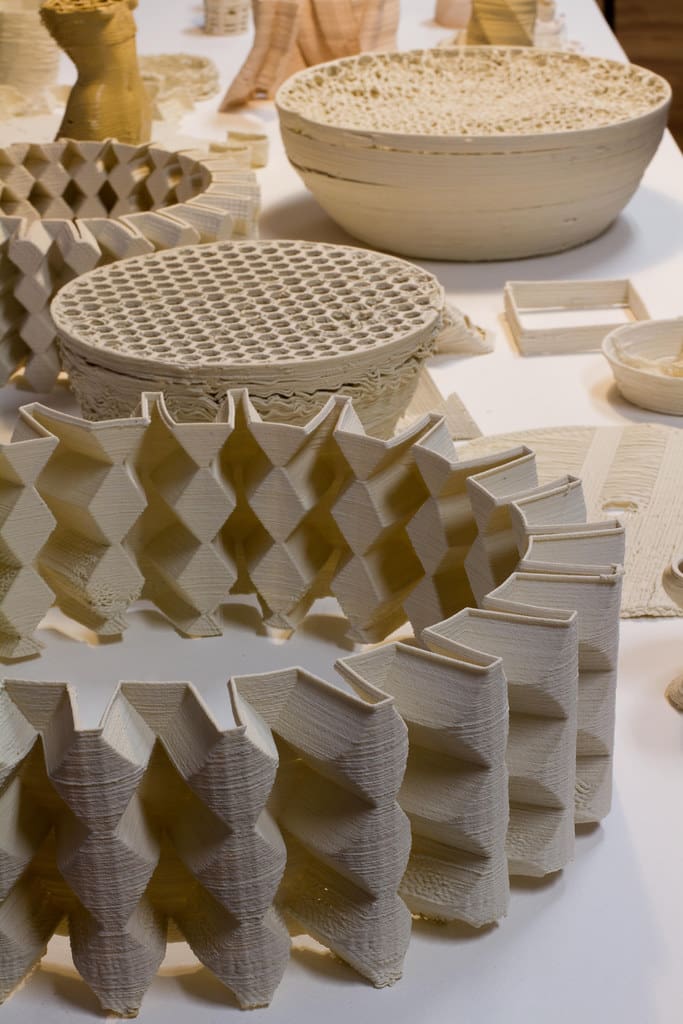
Advantages of Advanced Materials in 3D Printing
Enhanced Properties: Modern 3D printing materials are engineered to meet specific requirements such as higher strength, flexibility, or temperature resistance. Innovations in composite materials also allow for properties like electrical conductivity or translucency in printed objects.
Increased Productivity and Efficiency: Advanced materials can reduce the weight of components while maintaining strength, crucial for industries like automotive and aerospace where efficiency is paramount. Lightweight yet durable materials lead to more fuel-efficient vehicles and aircraft.
Customization and Complexity: With the advent of multi-material 3D printing, manufacturers can produce parts that combine different materials with varied properties in a single print cycle. This ability allows for complex, functional products customized to exact specifications without the need for assembly.
Sustainability: Many new materials designed for 3D printing are focused on sustainability. These include biodegradable plastics, recycled materials, and even organic-based filaments. Using these materials reduces waste and the environmental impact associated with manufacturing.
Cost Reduction: The development of more affordable and readily available printing materials reduces overall production costs. This democratization of materials makes 3D printing accessible to smaller businesses and individual consumers, fostering innovation at all levels.
Key Applications of Advanced Materials in 3D Printing
Aerospace and Automotive: High-performance materials like titanium and carbon fiber composites are used to produce lightweight parts that withstand extreme stress and temperatures, significantly enhancing the performance and efficiency of aircraft and vehicles.
Medical and Dental: Biocompatible materials enable the printing of custom prosthetics, implants, and dental devices. Innovations in bio-printing also allow for the creation of tissue and organ-like structures, which could revolutionize transplant medicine.
Electronics: Conductive materials are being developed for 3D printing circuit boards and electronic components. These materials enable the integration of electrical functionalities directly into printed parts, streamlining production processes and opening up new possibilities in design.
Construction: Concrete and other building materials are being adapted for 3D printing to construct buildings directly on-site, reducing material waste and construction costs while allowing for unprecedented design flexibility.
Fashion and Art: New flexible, durable, and aesthetically distinct materials are expanding the potential of 3D printing in fashion and the arts, allowing designers to create intricate patterns and structures that were previously impossible.

Challenges in Advanced Materials for 3D Printing
Material Development: Developing new materials that meet specific industrial standards is a complex, time-consuming, and costly process that requires extensive research and testing.
Compatibility and Standardization: Ensuring compatibility of new materials with existing 3D printing technologies and standardizing material properties for consistent quality and performance are ongoing challenges.
Technical Knowledge: Utilizing advanced materials effectively often requires specialized knowledge and skills, both in material science and 3D printing technology.
Regulatory Hurdles: Materials intended for use in industries like healthcare and aerospace must undergo rigorous regulatory approval processes, which can delay their introduction to the market.
Future Directions in 3D Printing Material Technology
The future of material technology in 3D printing is poised for significant growth, driven by continued innovation in material science. Anticipated developments include smarter materials with adaptive properties, greater use of sustainable and recyclable materials, and further advancements in the integration of electronics and biologically active components in printed structures.
Material technology in 3D printing is at the forefront of industrial innovation, offering transformative opportunities across diverse sectors. As new materials continue to emerge, they will expand the boundaries of what can be manufactured, driving forward the capabilities of 3D printing and opening up new realms of possibility. This ongoing evolution in materials not only enhances the utility and versatility of 3D printing but also underscores its role as a cornerstone technology in the future of manufacturing.