Textile engineering integrates the principles of engineering with specific knowledge of textile equipment and processes. This field is essential for the innovation and production of textiles used across various industries, including fashion, medical, automotive, and aerospace. 3D printing, also known as additive manufacturing, has emerged as a transformative technology in textile engineering, offering new ways to create textiles with complex designs and functionalities that were previously impossible or too costly to produce using traditional methods. This technology enables the fabrication of customized, high-performance textiles that can meet specific requirements of strength, flexibility, and aesthetic design.
The Emergence of 3D Printing in Textile Engineering
Initially used for prototyping and small-scale models, 3D printing has rapidly expanded its reach into textile engineering, driven by its potential to seamlessly integrate novel materials with traditional textile components. As the technology has evolved, it has allowed for the development of textiles that are not only structurally innovative but also functionally enhanced, opening up new applications in wearable technology, fashion design, and technical textiles.
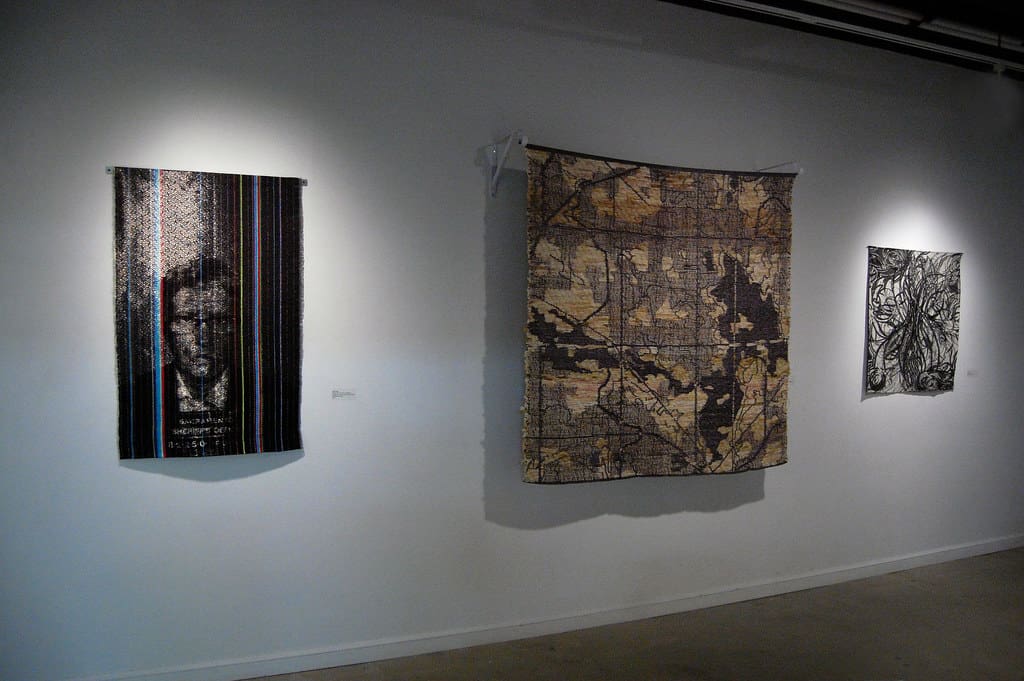
Advantages of 3D Printing in Textile Engineering
Innovative Design Possibilities: 3D printing enables the creation of complex textile structures that cannot be achieved through conventional weaving or knitting. This includes intricate lattices, seamless transitions between different materials, and integrated functionality such as conductivity or waterproofing.
Customization and Flexibility: Additive manufacturing allows for high levels of customization without significant increases in cost or production time, making it ideal for producing bespoke textiles for specialized applications.
Material Efficiency and Sustainability: 3D printing reduces waste by using only the amount of material needed to create the product, contributing to more sustainable manufacturing practices. It also opens the possibility of using recycled materials to further reduce environmental impact.
Rapid Prototyping and Production: The speed of 3D printing processes enables quick turnaround from design to final product, accelerating the development cycle and allowing for greater experimentation and innovation.
Key Applications of 3D Printing in Textile Engineering
Fashion and Apparel: 3D printing is used to create unique fashion items that feature complex designs and tailored functionalities. Designers can experiment with forms and structures that are not possible with traditional fabric-making techniques, pushing the boundaries of fashion design.
Performance and Technical Textiles: In sectors like sports and healthcare, 3D printing enables the development of performance-enhancing textiles, such as moisture-wicking fabrics, textiles with embedded sensors, and materials that can adapt to changes in temperature or pressure.
Medical Textiles: Customized implants, prosthetics, and supports made via 3D printing offer enhanced compatibility and functionality. Textiles with tailored properties can be designed to interface directly with human tissue, promoting better health outcomes.
Automotive and Aerospace: The automotive and aerospace industries benefit from lightweight and durable textile components that contribute to fuel efficiency and safety. 3D printing allows for the integration of high-performance fibers into composites used in vehicle and aircraft construction.
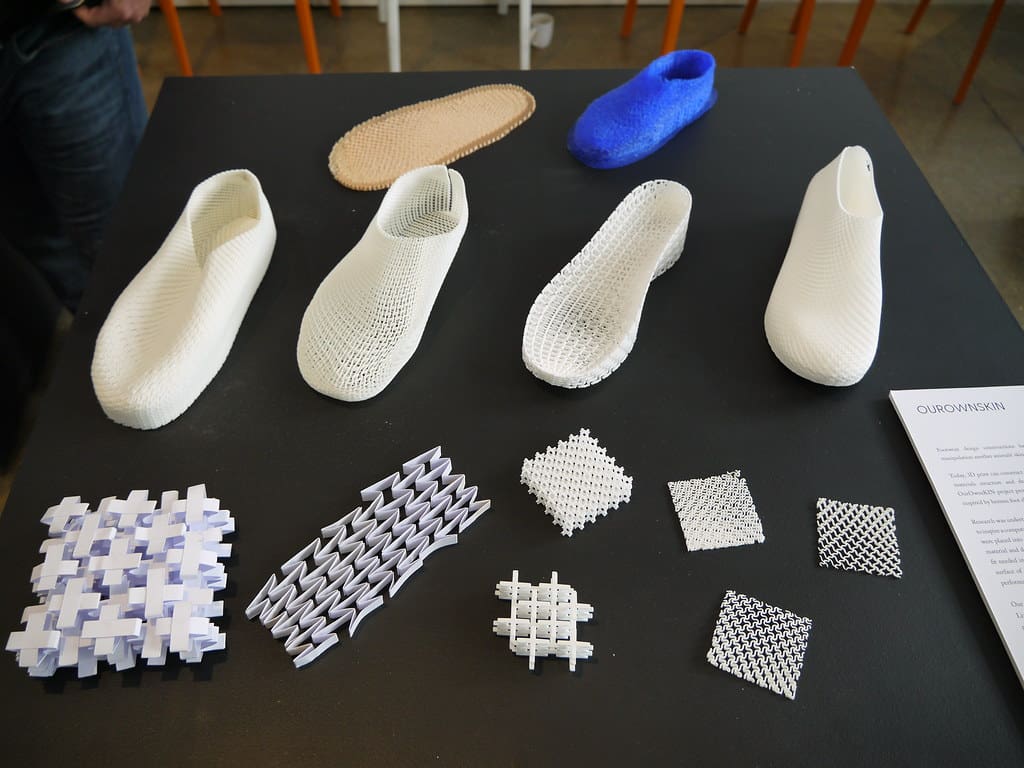
Challenges in 3D Printing for Textile Engineering
Material Limitations: The range of materials suitable for 3D printed textiles is still evolving. Developing materials that combine flexibility, durability, and other desirable properties while being suitable for printing is a major challenge.
Technical Complexity: The integration of 3D printing into existing textile manufacturing processes can be technically challenging, requiring significant adaptations in terms of machinery and software.
Scalability: While 3D printing is excellent for prototyping and small-batch production, scaling these processes to larger manufacturing volumes can be inefficient and costly with current technology.
Regulatory and Market Acceptance: For some applications, particularly in medical and protective textiles, 3D printed products must meet strict regulatory standards. Gaining market acceptance, especially in sectors with established production methods, can also be a hurdle.
Future Directions in 3D Printing for Textile Engineering
The future of 3D printing in textile engineering looks promising, with ongoing advancements likely to enhance its capabilities and applications. Anticipated developments include the creation of new materials that are more flexible, durable, and adaptable; improvements in printing technology that increase speed and reduce costs; and greater integration with traditional textile manufacturing processes.
3D printing is poised to revolutionize the field of textile engineering by enabling the production of textiles that combine novel aesthetics with enhanced functionalities. As the technology continues to evolve, it promises to open up new possibilities for the design and manufacturing of textiles, making it a pivotal tool in the development of next-generation fabrics. With ongoing research and development, 3D printing will increasingly become an integral part of textile engineering, reshaping how textiles are conceived, produced, and used across industries.