The shipbuilding industry, central to global commerce and naval defense, is undergoing a significant transformation driven by the integration of 3D printing technology. Also known as additive manufacturing, 3D printing offers unprecedented opportunities to enhance the design, production, and maintenance of ships. From cargo vessels to luxury yachts and naval ships, 3D printing is being leveraged to create complex components, streamline production processes, and foster innovation in ship design.
The Emergence of 3D Printing in Shipbuilding
Initially used for prototyping in various industries, 3D printing has rapidly expanded its capabilities to include the production of end-use products, notably in the aerospace and automotive sectors. The shipbuilding industry has begun to adopt this technology, recognizing its potential to produce highly customized, lightweight parts and to solve unique manufacturing challenges associated with traditional ship construction.
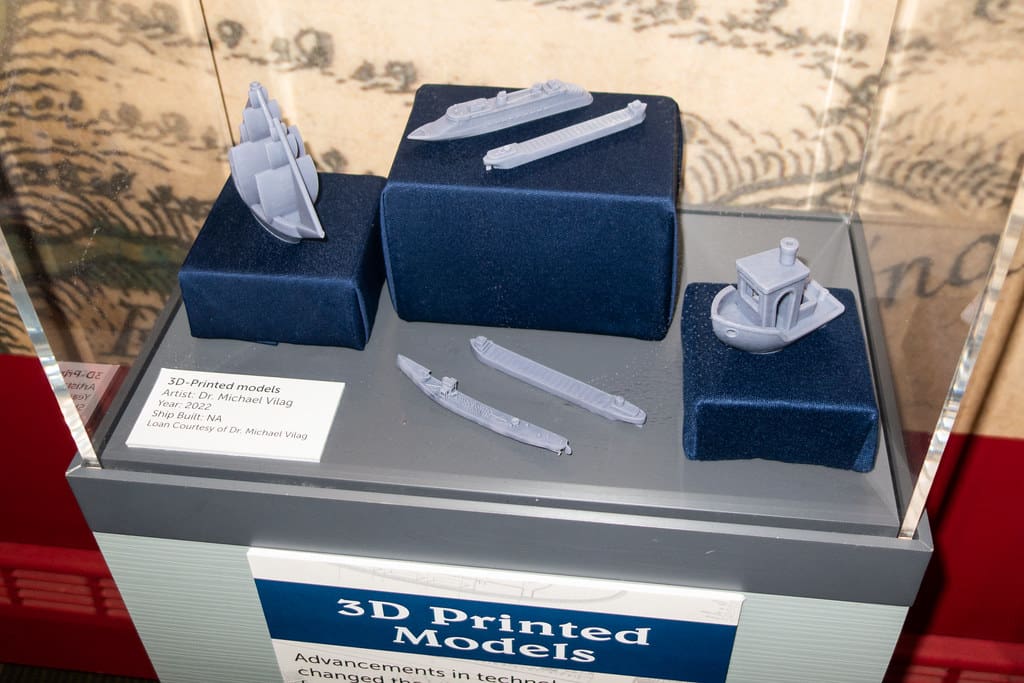
Advantages of 3D Printing in Ship Manufacturing
Customization and Complexity: 3D printing excels at creating complex geometries that traditional manufacturing methods struggle to achieve. This capability allows for the design of optimized structural components, intricate propellers, and customized interior fittings that enhance both the functionality and aesthetics of ships.
Weight Reduction: The ability to print with lightweight materials and hollow structures significantly reduces the overall weight of components. This weight reduction is crucial for improving fuel efficiency and cargo capacity, which are key concerns in ship operation and profitability.
Rapid Prototyping: 3D printing facilitates the quick development and testing of new ship designs and components, dramatically reducing the time from concept to construction. This speed enables shipbuilders to iterate designs more efficiently and respond more swiftly to market demands and regulatory changes.
Material Efficiency and Waste Reduction: Additive manufacturing minimizes material waste by using only the material necessary to build a part. This efficiency not only lowers material costs but also aligns with increasing environmental regulations aimed at reducing the ecological footprint of shipbuilding activities.
Supply Chain Simplification: By producing parts on-demand, 3D printing can streamline inventory management and reduce the need for extensive warehousing. This is especially beneficial for ships undergoing repairs or refurbishment, as replacement parts can be manufactured quickly and installed without lengthy delays.
Key Applications of 3D Printing in Ships
Structural Components and Hull Sections: Innovations in large-scale 3D printing have made it possible to produce larger structural components and even entire sections of ship hulls. These components can be optimized for strength and durability, transforming how ships are built.
Propulsion Systems: 3D printing allows for the production of more efficient propeller blades and components of propulsion systems. These parts can be designed with complex geometries that enhance hydrodynamic efficiency and reduce noise and vibration.
Interior Design and Customization: Luxury cruise ships and private yachts benefit from the ability to create bespoke interior designs and luxury fittings, all tailored to individual specifications and preferences. This customization extends to ergonomic furniture, decorative elements, and functional cabin components.
Repair and Maintenance Tools: Ships can carry 3D printers onboard, allowing crews to produce necessary tools and parts on-demand during long voyages. This capability is invaluable for maintaining operational readiness and reducing downtime due to equipment failure.

Challenges in 3D Printing for Ships
Despite its potential, the adoption of 3D printing in the shipbuilding industry faces several challenges:
Material Durability: Ensuring that 3D-printed materials are durable enough to withstand the harsh marine environment, including exposure to saltwater, intense UV radiation, and extreme weather conditions, remains a challenge.
Scale Limitations: While 3D printing technology continues to advance, scaling up to produce large ship components efficiently and economically poses significant technical and logistical challenges.
Regulatory and Certification Issues: Ships must meet stringent safety and performance standards. Obtaining certification for 3D-printed components, especially those critical to structural integrity and safety, involves rigorous testing and regulatory review.
Future Directions in 3D Printing for Ships
The future of 3D printing in shipbuilding looks promising, with ongoing advancements in printer technologies, materials science, and design software expected to address current limitations. As these innovations mature, 3D printing is likely to become an integral part of ship manufacturing, offering more sustainable, efficient, and cost-effective solutions.
3D printing is poised to continue its transformative impact on the shipbuilding industry, reshaping traditional practices and introducing new levels of efficiency and customization. As the technology evolves, it promises to unlock new possibilities in ship design and construction, enhancing the capabilities and reducing the environmental impact of maritime vessels around the world.