The aerospace industry stands at the forefront of technological advancements, with 3D printing playing a pivotal role in revolutionizing airplane manufacturing. This innovative manufacturing approach, known as additive manufacturing, allows for the creation of complex, lightweight components that are crucial for enhancing the performance and efficiency of aircraft. As aerospace companies strive to meet demands for higher fuel efficiency, reduced emissions, and lower costs, 3D printing emerges as a key technology, enabling faster development cycles, greater customization, and improved component performance.
The Emergence of 3D Printing in Airplane Manufacturing
3D printing has evolved from producing simple prototypes to manufacturing critical, load-bearing components used in the aerospace industry. This technology’s ability to handle complex designs and high-strength materials has made it an integral part of the production process for both commercial and military aircraft. The adoption of 3D printing in the aerospace sector is driven by its potential to reduce weight, cut production costs, and decrease waste, aligning with the industry’s goals of sustainability and efficiency.

Advantages of 3D Printing in Airplanes
Weight Reduction: One of the most significant benefits of 3D printing is its ability to produce lightweight structures. Aerospace engineers can design parts with complex, hollow interiors or lattice structures that are not possible with traditional manufacturing methods, significantly reducing the weight of the aircraft without compromising strength.
Complex Geometries: 3D printing excels at creating intricate geometries that optimize aerodynamics and improve the functionality of various components. This capability allows for the integration of multiple features into a single part, reducing the number of components needed in an assembly.
Material Efficiency: Additive manufacturing minimizes material waste by using only the material necessary to build a part, in contrast to traditional subtractive manufacturing methods, which cut away significant material from solid blocks.
Customization and Rapid Prototyping: 3D printing offers unparalleled flexibility in customizing parts for specific applications and enables rapid prototyping of new designs. This is particularly beneficial in the development of experimental aircraft and for tailoring components to suit unique operational requirements.
Key Applications of 3D Printing in Airplanes
Engine Components: Advanced metal 3D printing techniques are used to produce complex engine parts, including fuel nozzles and turbine blades. These components benefit from the technology’s ability to create fine internal channels and structures that enhance fuel efficiency and engine performance.
Structural Components: Airframe parts such as brackets, panels, and even critical structural components are being manufactured with 3D printing. These parts often feature optimized designs that reduce weight while maintaining or enhancing strength and durability.
Cabin Interiors: From customized seat frames to intricate air ducts and overhead bin latches, 3D printing is used to create lightweight and durable cabin components that enhance passenger comfort and optimize space usage.
Tooling and Ground Support Equipment: 3D printing is also revolutionizing the production of tooling and ground support equipment. Custom tools, jigs, and fixtures can be produced quickly and cost-effectively, reducing lead times and improving maintenance operations.
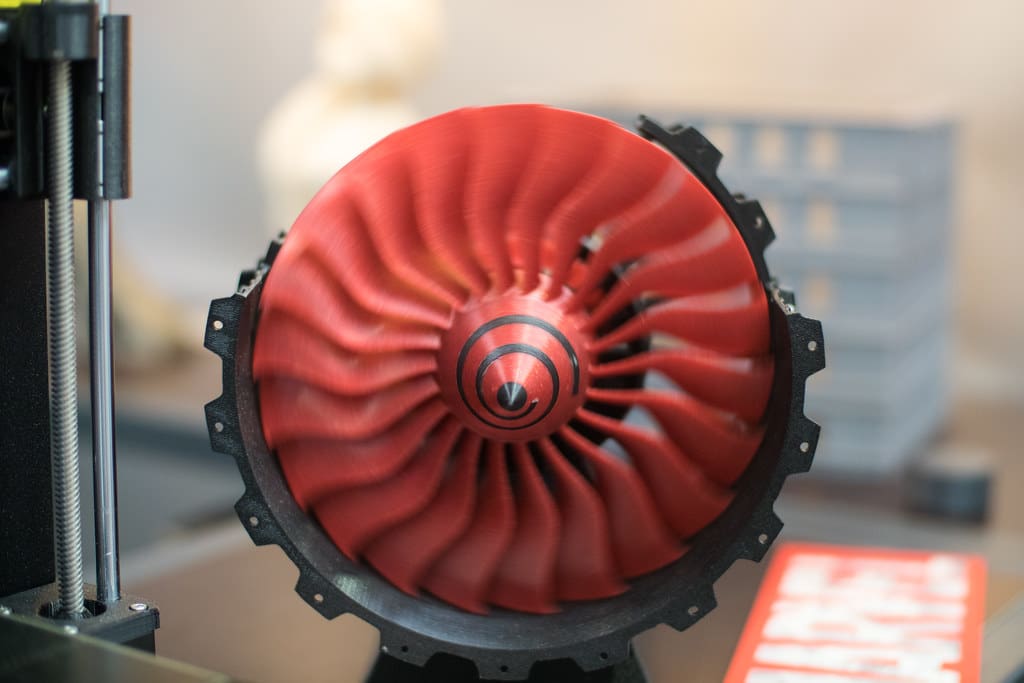
Challenges in 3D Printing for Airplanes
Despite its numerous advantages, the application of 3D printing in airplane manufacturing faces several challenges:
Material Properties: Ensuring that 3D-printed materials meet stringent aerospace standards for durability, heat resistance, and fatigue life is crucial. The development of new materials that can withstand the harsh environmental conditions experienced by aircraft is ongoing.
Certification and Standardization: Obtaining certification for 3D-printed aerospace components is a complex and time-consuming process. Ensuring that these components comply with international aviation standards is critical for their widespread adoption.
Production Scale: While 3D printing is highly effective for small-batch production and prototyping, scaling up to mass production levels required by commercial aviation presents logistical and economic challenges.
Future Directions in 3D Printing for Airplanes
The future of 3D printing in airplane manufacturing looks promising, with continuous advancements in 3D printing technologies, materials, and digital design tools expected to overcome current limitations. As these technologies mature, 3D printing is likely to become even more integrated into mainstream aerospace manufacturing, leading to more efficient, sustainable, and cost-effective aircraft production.
3D printing is poised to continue its transformative impact on airplane manufacturing, offering significant benefits in terms of design flexibility, weight reduction, and material efficiency. As the technology evolves, it promises to play a crucial role in shaping the future of the aerospace industry, driving innovations that enhance aircraft performance, reduce environmental impact, and revolutionize production processes.