Optomechanical engineering, a specialized field at the intersection of optics and mechanical engineering, deals with the design and manufacture of mechanical systems that interact with light, such as lenses, mirrors, and optical mounts. The advent of 3D printing technology is bringing a transformative approach to this field, offering new possibilities for designing and producing complex optomechanical components with unprecedented precision and flexibility.
The Emergence of 3D Printing in Optomechanical Engineering
3D printing, also known as additive manufacturing, has evolved from creating simple prototypes to manufacturing sophisticated, functional components suitable for use in high-precision fields like optomechanics. This technology allows for the direct fabrication of complex geometries that are often challenging or impossible to achieve with traditional manufacturing methods. The ability to integrate multiple functions and materials into a single manufacturing process is particularly beneficial in optomechanical engineering, where component alignment and stability are critical.
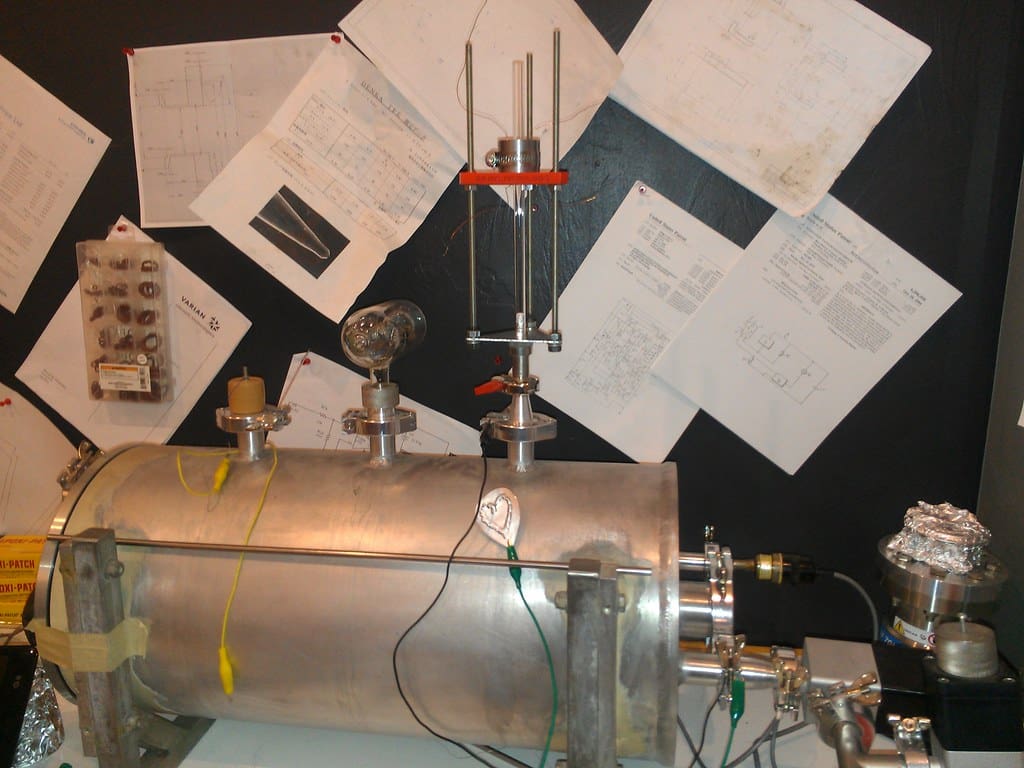
Advantages of 3D Printing in Optomechanical Engineering
Complex Geometries and Integrated Designs: 3D printing excels at producing intricate designs that traditional machining struggles to achieve. This capability is crucial for creating optomechanical components with complex internal structures or integrated features for alignment, stabilization, and mounting of optical elements.
Rapid Prototyping and Iteration: The technology enables quick turnaround times from design to prototype, allowing engineers to iterate designs swiftly and efficiently. This rapid prototyping significantly accelerates the development of optomechanical systems, facilitating faster innovation and problem-solving.
Customization and Scalability: 3D printing offers unparalleled customization without the need for expensive tooling or setup changes, making it ideal for producing bespoke optomechanical components. Additionally, it provides scalability from one-off prototypes to small production runs economically.
Material Diversity: Advanced 3D printing technologies can process a wide range of materials, including plastics, metals, and composites. This diversity allows engineers to choose materials based on specific properties needed for optomechanical applications, such as thermal stability, mechanical strength, and light absorption.
Key Applications of 3D Printing in Optomechanical Engineering
Optical Mounts and Assemblies: 3D printing is used to create highly customized optical mounts and assemblies that require precise alignment and stability. These components can be designed to minimize vibrations and thermal expansion, which are crucial for maintaining the performance of optical systems.
Lens Holders and Barrels: The production of lens holders and barrels benefits from 3D printing’s ability to accommodate complex designs and tight tolerances. These components often require precise geometries to ensure the correct positioning and orientation of lenses within optical devices.
Adaptive Optics Components: Components for adaptive optics systems, which require customization and flexibility, are ideally suited for 3D printing. These systems often include deformable mirrors and mounts that can be rapidly prototyped and refined using additive manufacturing.
Lightweight Structures for Aerospace and Satellite Applications: In aerospace applications, minimizing weight while maintaining structural integrity is paramount. 3D printed optomechanical components can be designed with internal lattice structures that reduce weight without compromising strength or stability.

Challenges in 3D Printing for Optomechanical Engineering
Despite its potential, several challenges need to be addressed to fully harness the benefits of 3D printing in optomechanical engineering:
Surface Finish and Precision: Many optical applications require extremely smooth surface finishes and high precision. Achieving these characteristics with 3D printing often necessitates post-processing steps, which can add time and cost to the manufacturing process.
Material Properties: Ensuring that 3D printed materials meet the exact requirements of optomechanical applications, such as optical clarity, thermal expansion coefficients, and mechanical durability, remains a challenge.
Regulatory and Standardization Issues: The optomechanical engineering field often involves stringent regulatory requirements, especially in medical and aerospace applications. Developing standards and obtaining certification for 3D printed optomechanical components can be complex and time-consuming.
Future Directions in 3D Printing for Optomechanical Engineering
The future of 3D printing in optomechanical engineering looks promising, with continuous advancements in printer technologies, materials, and design software expected to mitigate current limitations. Innovations in hybrid manufacturing processes that combine additive and subtractive methods could further enhance the capabilities of 3D printing, allowing for the production of components with the required precision and surface finishes.
3D printing is poised to revolutionize optomechanical engineering by offering enhanced capabilities for designing and manufacturing complex, customized components efficiently and sustainably. As the technology continues to evolve, it promises to unlock new possibilities in the fabrication of precision optical systems, potentially transforming industries ranging from telecommunications to healthcare.