Control engineering, a pivotal discipline within systems engineering that focuses on modeling, designing, and implementing controllers to manage dynamic systems, is seeing transformative changes with the introduction of 3D printing technology. This innovation is revolutionizing the way control systems are conceptualized, developed, and deployed, offering unprecedented precision and customization in component manufacturing and system integration.
The Emergence of 3D Printing in Control Engineering
Traditionally reliant on standard manufacturing techniques for system components and housings, control engineering has embraced 3D printing to overcome limitations associated with conventional processes. 3D printing, or additive manufacturing, enables the rapid prototyping and production of intricate parts required for advanced control systems, facilitating enhanced functionality and system performance.
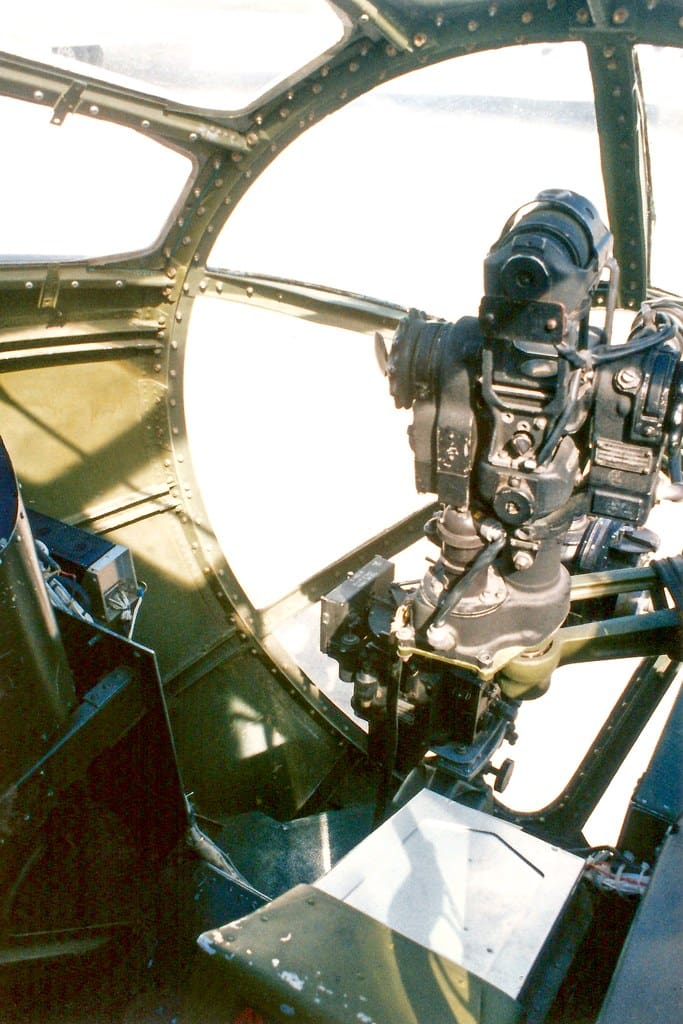
Advantages of 3D Printing in Control Engineering
Customization and Complexity: 3D printing allows for the creation of complex component geometries that are perfectly tailored to specific control applications. This capability is crucial for systems requiring high levels of integration and compactness, such as aerospace control systems or intricate robotic controllers.
Rapid Prototyping: The speed of 3D printing accelerates the development cycle of control systems. Engineers can design, iterate, and refine components quickly and cost-effectively, significantly shortening the time from concept to deployment.
Integration Flexibility: 3D printing provides the ability to integrate multiple functions and components into single, cohesive units. This integration is particularly beneficial in reducing the size and weight of control systems, crucial for applications in mobile and field-deployed devices.
Cost Efficiency: By minimizing material waste and eliminating the need for multiple fabrication steps, 3D printing reduces the overall cost of producing control system components. It also opens up the possibility of low-volume or bespoke production runs without the associated high costs.
Key Applications of 3D Printing in Control Engineering
Custom Control Devices and Panels: 3D printing is ideal for fabricating custom control panels and interfaces tailored to specific user requirements or operating environments. This application is particularly valuable in industrial automation, where control systems must align precisely with plant operations and processes.
Sensor and Actuator Housing: Sensors and actuators are integral to control systems, monitoring and executing the control actions necessary for system stability and performance. 3D printing allows for the production of custom housings that protect these components while optimizing their functionality and integration with other system parts.
Robotic Systems: In robotics, control systems are central to machine performance and versatility. 3D printing facilitates the rapid development of robotic components that are lightweight, strong, and highly integrated, enhancing the robot’s functionality and adaptability.
Aerospace and Automotive Applications: These sectors demand high-performance control systems with components that can withstand extreme conditions. 3D printing is used to produce parts that meet these rigorous standards, including those for unmanned aerial vehicles (UAVs) and vehicle stability control systems.

Challenges in 3D Printing for Control Engineering
Despite its significant advantages, 3D printing in control engineering faces several challenges:
Material Limitations: Finding materials that can meet the stringent requirements of control engineering, such as thermal stability, electrical insulation, and mechanical strength, is often challenging.
Precision and Reliability: The precision and reliability of 3D printed components must match or exceed those of traditionally manufactured parts, especially in control systems where safety is paramount.
Scaling Issues: While 3D printing is excellent for prototypes and small production runs, scaling up to larger volumes can be economically and technically challenging, particularly when consistency and quality control are critical.
Future Directions in 3D Printing for Control Engineering
The future of 3D printing in control engineering looks promising, with ongoing advancements in printing technologies, materials, and digital design tools. Continued innovation is expected to address current challenges, making 3D printing even more viable for a broader range of applications in control engineering. Additionally, the integration of 3D printing with emerging technologies such as IoT and AI could further enhance the capabilities and efficiency of control systems.
3D printing is poised to revolutionize control engineering by offering enhanced capabilities for designing and manufacturing precise, integrated, and customizable control systems. As the technology continues to evolve, it promises to enable new levels of innovation and efficiency in the field, leading to smarter, more responsive control solutions across various industries. Embracing 3D printing in control engineering not only streamlines production processes but also opens up new possibilities for system design and functionality.