Electronic engineering is crucial in driving innovations across various sectors, from consumer electronics to advanced communication systems. With the advent of 3D printing, the field is witnessing a transformation in how electronic components, circuits, and devices are designed and manufactured. This technology enables the rapid prototyping and production of complex, custom-designed electronics with unprecedented precision and efficiency.
The Emergence of 3D Printing in Electronic Engineering
3D printing, or additive manufacturing, initially found its application in creating prototypes but has evolved to include the production of functional electronic components and assemblies. This shift has been facilitated by advances in 3D printing technologies that allow for the integration of conductive materials, substrates, and insulation within a single manufacturing process. Today, 3D printing is revolutionizing electronic engineering by enabling the production of more compact, efficient, and innovative electronic solutions.

Advantages of 3D Printing in Electronic Engineering
Design Flexibility and Complexity: 3D printing allows engineers to overcome traditional manufacturing constraints, enabling the design and production of electronics with complex geometries and improved functionalities. This flexibility is particularly beneficial for developing integrated systems and miniaturized electronics.
Rapid Prototyping and Speed to Market: The ability to quickly produce prototypes and iterate designs without the need for costly tooling and setup accelerates the development process, significantly reducing the time from concept to market.
Customization: 3D printing supports the customization of electronic components and devices at no additional production cost, which is invaluable for applications requiring unique specifications or for small production runs of specialized equipment.
Material Efficiency and Sustainability: By depositing material only where it is needed, 3D printing minimizes waste compared to traditional subtractive manufacturing processes, contributing to more sustainable manufacturing practices.
Key Applications of 3D Printing in Electronic Engineering
Printed Circuit Boards (PCBs): 3D printing is changing the paradigm of PCB manufacturing by enabling the direct printing of multi-layer circuits with conductive inks. This capability allows for the creation of more compact and complex circuitry designs, crucial for modern electronic devices.
Antennas and RF Components: Engineers are utilizing 3D printing to produce antennas and other radio frequency (RF) components with precise, application-specific designs. These components often require complex shapes that are difficult to achieve with conventional manufacturing methods.
Sensors and Actuators: The production of sensors and actuators via 3D printing allows for greater integration and miniaturization. These devices can be tailored to precise operational requirements for applications ranging from robotics to wearable technology.
Flexible and Wearable Electronics: 3D printing is ideal for developing flexible electronics that can conform to various shapes and surfaces. This flexibility is particularly important for wearable devices, where electronics need to integrate seamlessly with user movements and ergonomic requirements.
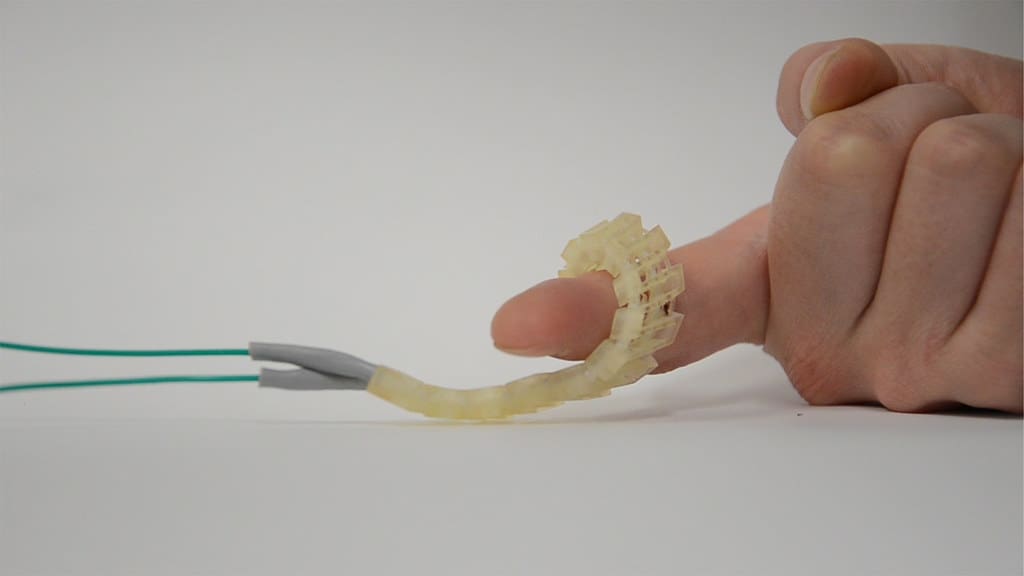
Challenges in 3D Printing for Electronic Engineering
Despite its many advantages, 3D printing faces specific challenges in electronic engineering:
Material Conductivity and Performance: While there have been significant advancements in conductive inks and materials for 3D printing, achieving the level of conductivity required for some high-performance electronic components remains a challenge.
Precision and Reliability: Ensuring the precision and long-term reliability of 3D-printed electronic components is critical, especially for applications in critical systems. Ongoing developments are needed to improve the accuracy and durability of printed electronics.
Integration with Existing Manufacturing Processes: Fully integrating 3D printing into existing electronic manufacturing processes poses logistical and technical challenges. Combining traditional and additive manufacturing methods effectively requires careful planning and adaptation.
Future Directions in 3D Printing for Electronic Engineering
The future of 3D printing in electronic engineering is promising, driven by continuous innovations in 3D printing technologies and materials. Researchers are focused on developing higher conductivity materials, more reliable printing techniques, and seamless integration with traditional electronic manufacturing processes. The ongoing miniaturization of electronic components and the demand for more personalized electronic solutions are likely to further accelerate the adoption of 3D printing in this field.
3D printing is poised to revolutionize electronic engineering by offering enhanced capabilities for designing and manufacturing advanced electronic components and devices. As the technology continues to evolve, it promises to foster new levels of innovation in electronics, leading to smarter, more efficient, and customizable solutions. Embracing 3D printing in electronic engineering not only streamlines production processes but also opens up new possibilities for technological advancement.