Digital Light Processing (DLP) 3D printing is a sophisticated form of additive manufacturing that uses light to cure photopolymeric resins into solid objects. Originating from the same technology used in digital projectors, DLP utilizes a digital micromirror device (DMD) to project images of each layer across the entire platform, significantly speeding up the printing process.
How DLP Printing Works
DLP technology stands out for its use of a digital projector to cure photopolymer resins. The process begins with a vat of liquid photopolymer resin, which is sensitive to light. The digital projector, which employs thousands of tiny mirrors, directs UV light onto the surface of the resin, hardening it precisely where the object is to be formed. The build platform then moves down incrementally, and the projector flashes the next image layer. Because each entire layer is exposed all at once, DLP can produce complex parts more quickly than point-by-point methods like stereolithography (SLA).
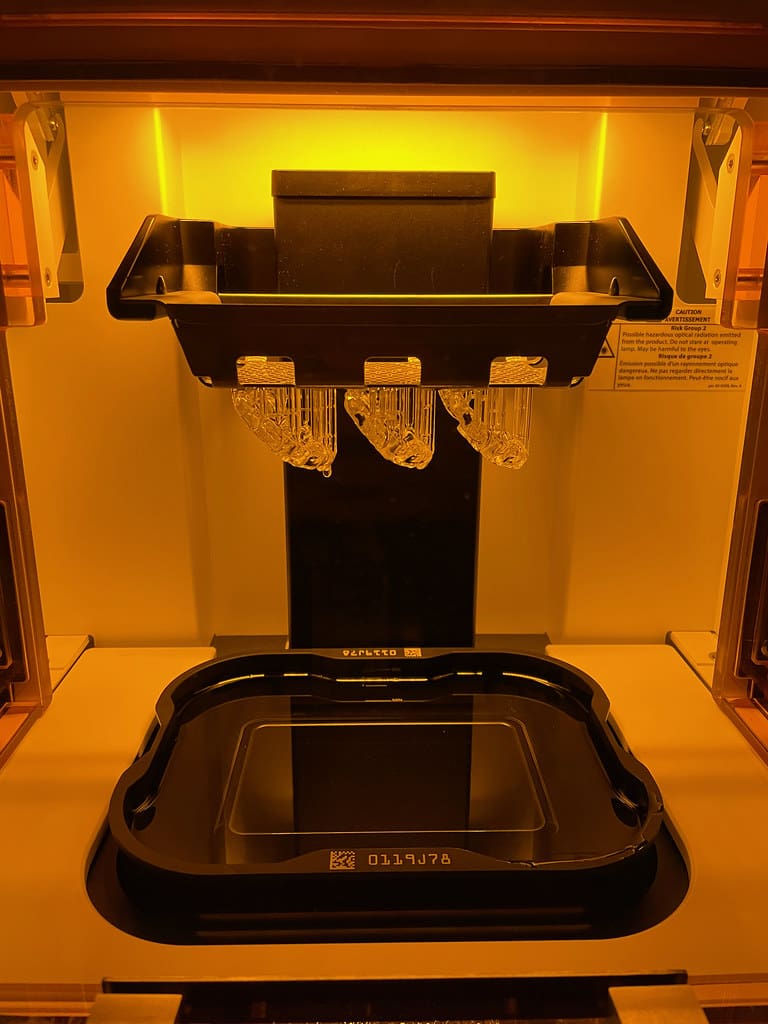
One of the critical benefits of DLP is its remarkable precision and resolution, thanks to the projector’s ability to control the image down to individual pixels. This capability allows for intricate details and smooth finishes that are ideal for small, complex objects.
Advantages of DLP 3D Printing
Speed: DLP’s method of curing entire layers simultaneously allows it to operate faster than many other resin-based 3D printing technologies.
Precision: The use of a digital projector enables DLP to achieve fine details and complex geometries with high accuracy, making it suitable for applications that demand precise dimensional tolerances.
Efficiency: DLP printers efficiently use materials by recycling unused resin, and scaling production does not significantly impact time, making it cost-effective for higher volumes.
Applications of DLP 3D Printing
DLP printing is highly favored in several industries:
Dental Industry: For creating dental implants and crowns that require precise measurements and smooth surfaces to fit comfortably.
Jewelry Manufacturing: Enables the creation of intricately detailed jewelry designs that would be difficult or impossible to achieve through traditional methods.
Prototyping: Particularly useful in the medical, consumer electronics, and automotive industries, where high detail and surface quality are crucial for testing the form and fit of new products.
Considerations and Limitations
Despite its many benefits, DLP 3D printing comes with its own set of challenges:
Material Limitations: The range of compatible materials is generally narrower than in FDM or SLS printing, largely limited to different types of photopolymer resins.
Post-Processing: Completed prints often require extensive cleaning to remove excess resin, followed by post-curing in UV light to reach final strength and stability.
Durability Concerns: Standard DLP resins may not match the mechanical strength and thermal resistance of materials used in other forms of 3D printing, which can limit their use in functional parts.
The Future of DLP Printing
The future of DLP looks promising with continuous advancements in projector technology and resin chemistry. Researchers are developing new, more durable resins that could broaden DLP’s applications, potentially including more functional parts and expanded use in mass production. Improvements in projector efficiency and resolution could also further enhance the detail and speed of DLP printing.
Digital Light Processing (DLP) 3D printing offers a combination of speed, precision, and efficiency, making it a valuable tool for industries requiring detailed and complex components. As technology continues to advance, the potential applications of DLP will expand, making it an even more attractive option for a wide range of professional uses. Whether for rapid prototyping or the production of final products, DLP 3D printing is a technology that promises to drive innovation in various fields.