3D printing, also known as additive manufacturing, has revolutionized how products are designed, prototyped, and produced across various industries. This innovative technology allows for the creation of complex, customized items directly from digital designs, offering unprecedented flexibility and speed in manufacturing.
The 3D Printing Processes
Digital Design
The first step in the 3D printing process involves creating or obtaining a digital model, typically crafted using Computer-Aided Design (CAD) software. For objects that already exist physically, 3D scanners can be used to capture their dimensions accurately, creating a digital replica. The design stage is crucial as it directly influences the aesthetics, functionality, and manufacturability of the final product.
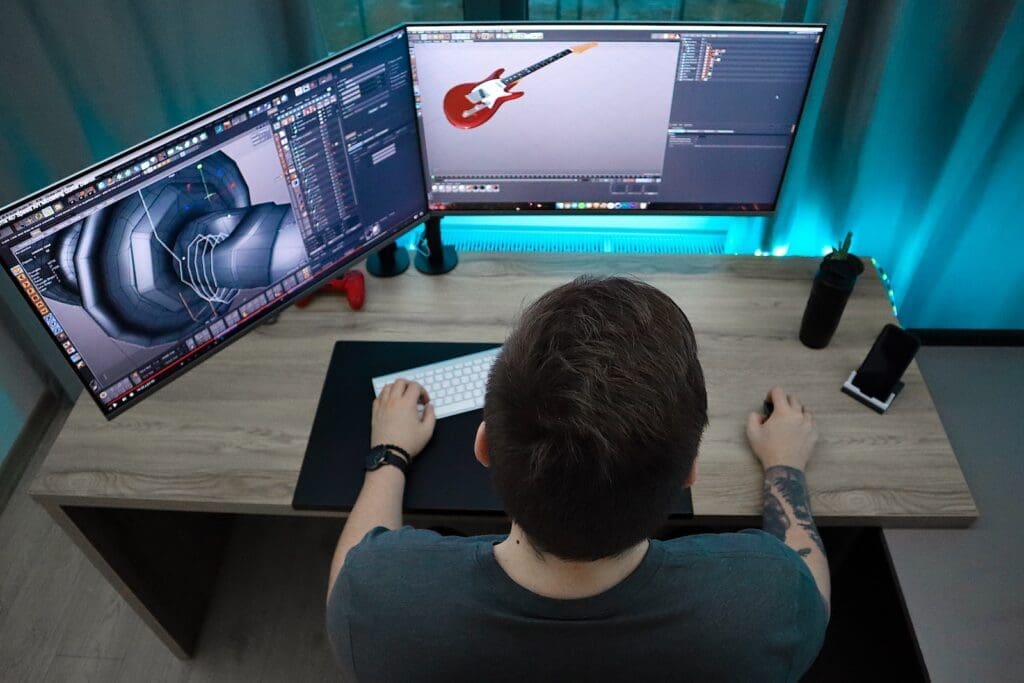
Slicing the Model
Once the digital model is ready, it must be prepared for the 3D printer. This is done using slicing software, which converts the 3D model into a series of thin, horizontal layers—essentially creating a comprehensive blueprint for the printer. The software allows the user to adjust settings such as layer thickness and printing speed, which can impact the print quality and time required to print the object.

Material Selection
Choosing the appropriate material is vital for the success of the printing process. 3D printers can use a variety of materials, including but not limited to plastics, resins, metals, and ceramics. Each material has specific properties that make it suitable for different applications; for instance, plastics are commonly used for prototypes, while metals are preferred for industrial parts due to their strength.
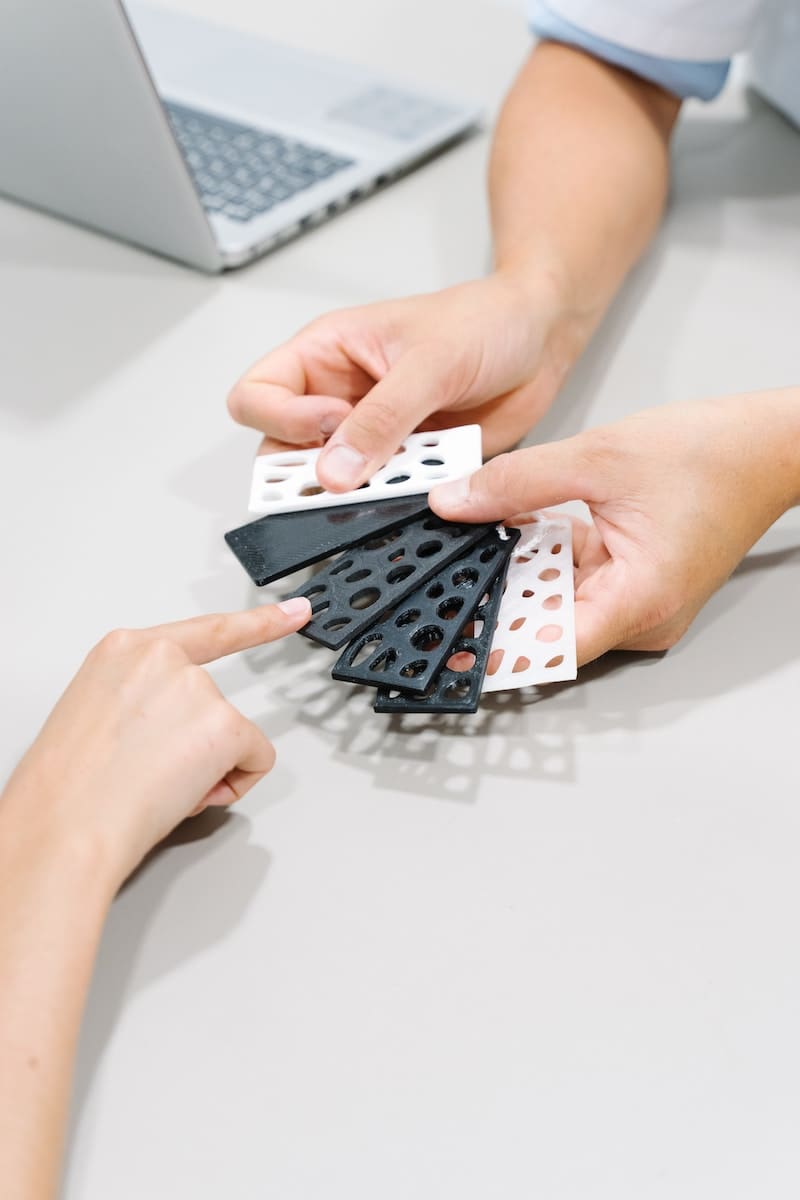
Preparing the 3D Printer
Before printing can begin, the printer itself must be prepared. This includes calibrating the machine, loading the selected material, and ensuring that the build platform is properly aligned. This stage is critical to ensure the accuracy and quality of the finished product.
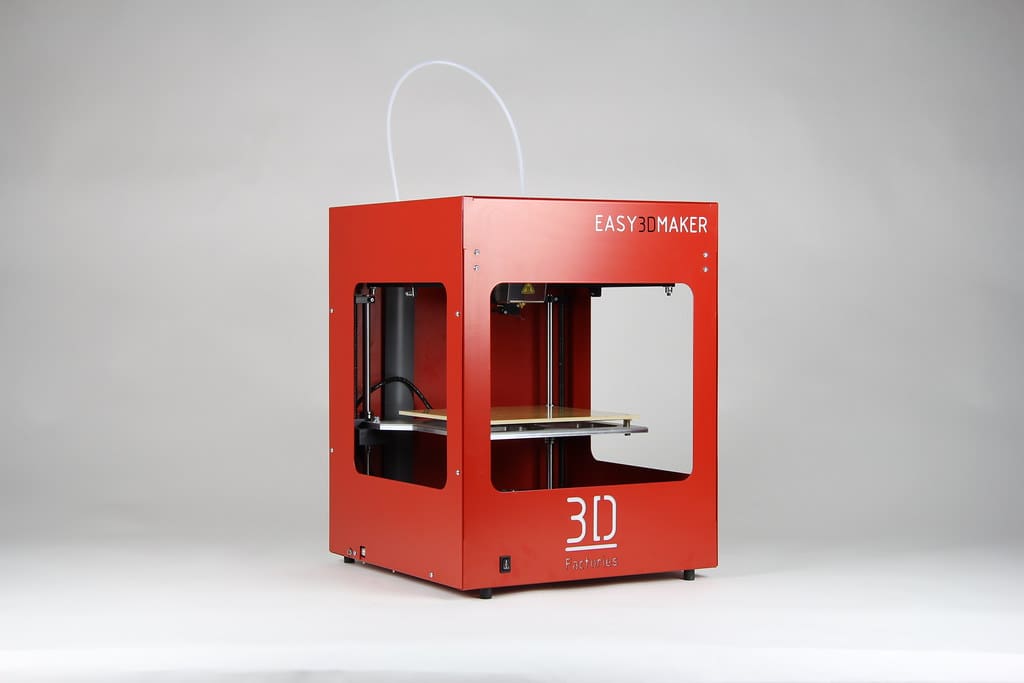
Printing Layer by Layer
The 3D printer creates the object by depositing material layer by layer from the bottom up. Each layer corresponds to a cross-section of the final object, as defined in the slicing stage. Depending on the printer and the material used, this could involve melting filament to form layers (Fused Deposition Modeling), curing liquid resin with UV light (Stereolithography), or selectively sintering powder (Selective Laser Sintering).
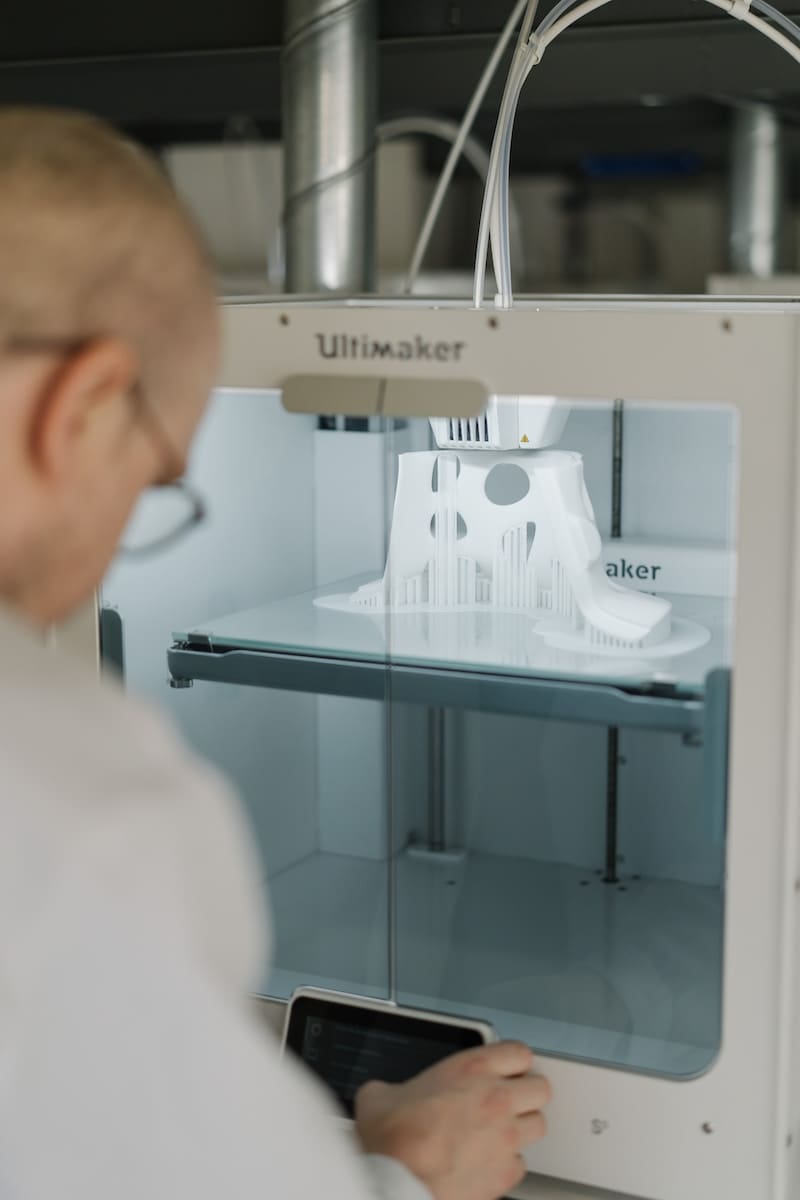
Building Up the Object
As layers are added, the object begins to take shape. The process requires precise control of temperature and speed to ensure that each layer adheres properly to the one below without defects.
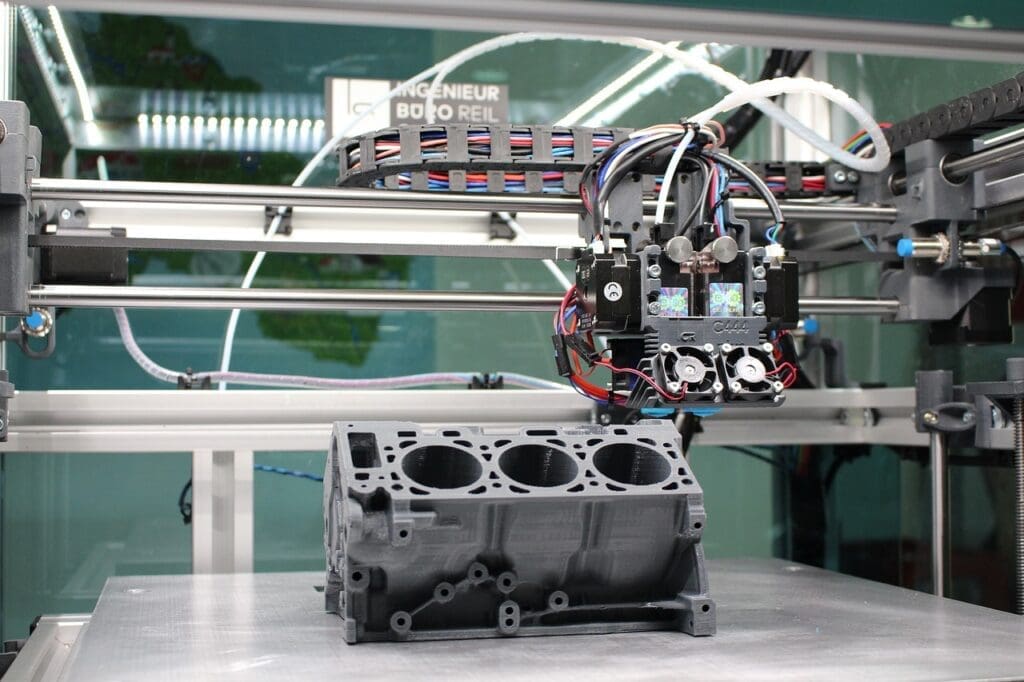
Support Structures
For overhanging designs or parts with complex geometries, support structures may be necessary. These are additional, often temporary, structures printed to support the object during printing. They must be removed in post-processing, which can sometimes be labor-intensive.
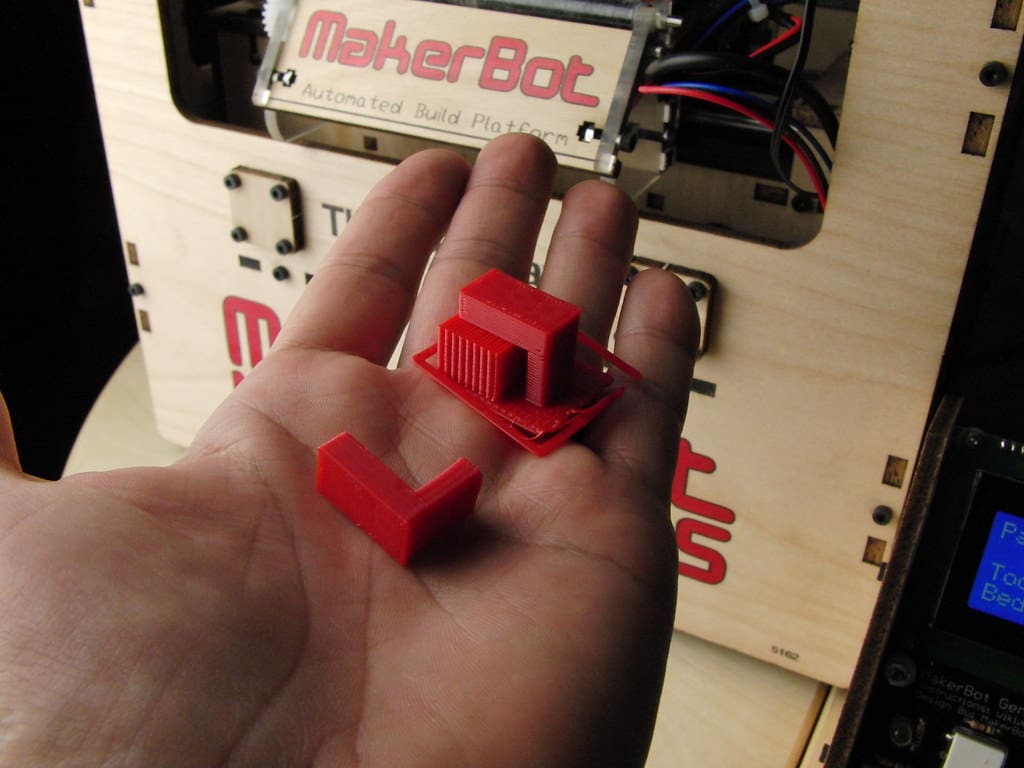
Finishing Touches
After the object is printed, post-processing is required to achieve the desired finish. This might include sanding to smooth the surface, removing support structures, and applying paint or sealant to enhance appearance and durability.
Advancements and Future Potential
3D printing technology is continually advancing, with improvements in speed, material variety, and print quality. Recent innovations include multi-material printing and enhanced precision, which open new possibilities for customization and functionality. Looking ahead, 3D printing is expected to play a significant role in mass customization, medical implants, and even construction, potentially transforming traditional manufacturing paradigms.
Understanding the 3D printing process is essential for anyone involved in design, engineering, or manufacturing. This technology not only enables rapid prototyping and complex designs but also promises a future where digital fabrication is mainstream. As 3D printing technology continues to evolve, it will likely become an even more integral part of our approach to building and creating in the 21st century.
3D printing transforms digital design into solid objects. Beginning with a digital model created through Computer-Aided Design (CAD) software, the model is then sliced into numerous layers. These digital slices serve as a guide for the 3D printer, which deposits material layer by layer to construct the final object. Various materials, including plastics, metals, and ceramics, can be utilized based on the intended application.
The process, known as additive manufacturing, allows for intricate designs, rapid prototyping and customization. 3D printing has revolutionized industries, from healthcare to aerospace, offering unparalleled flexibility in manufacturing and design.