3D printing, also known as additive manufacturing, is a process that creates physical objects from a digital design by layering materials. Since its development in the 1980s, 3D printing has revolutionized prototyping and manufacturing across various industries. From creating intricate jewelry to building rocket parts, the capabilities of 3D printing are vast and continue to expand.
History of 3D Printing
The journey of 3D printing began in 1984 with Charles Hull’s invention of stereolithography, a technique that allowed objects to be created layer by layer using photopolymer resin. This innovation led to the development of the first 3D printer. Since then, the technology has evolved rapidly, with new techniques and materials being introduced, expanding its application from industrial manufacturing to everyday use at home.
How 3D Printing Works
3D printing starts with a digital model, typically created using computer-aided design (CAD) software. The printer then builds the object layer by layer. There are several types of 3D printing technologies:
Fused Deposition Modeling (FDM)
This method uses a thermoplastic filament that is heated and extruded through a nozzle to form layers.
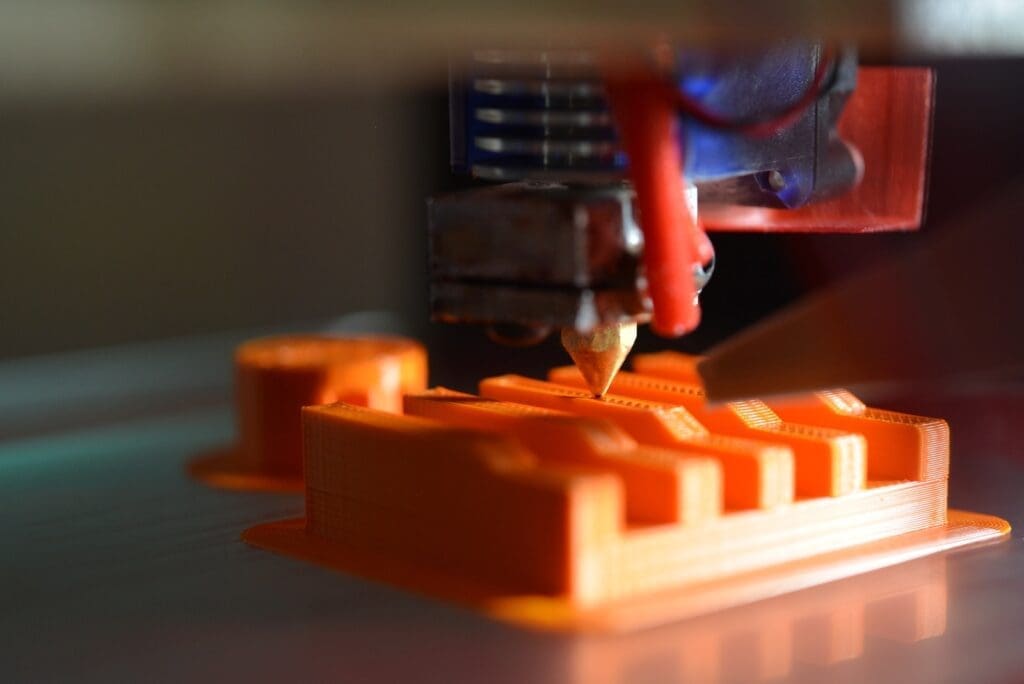
Stereolithography (SLA)
Stereolithography uses an ultraviolet laser to harden liquid resin into plastic in a precise pattern.
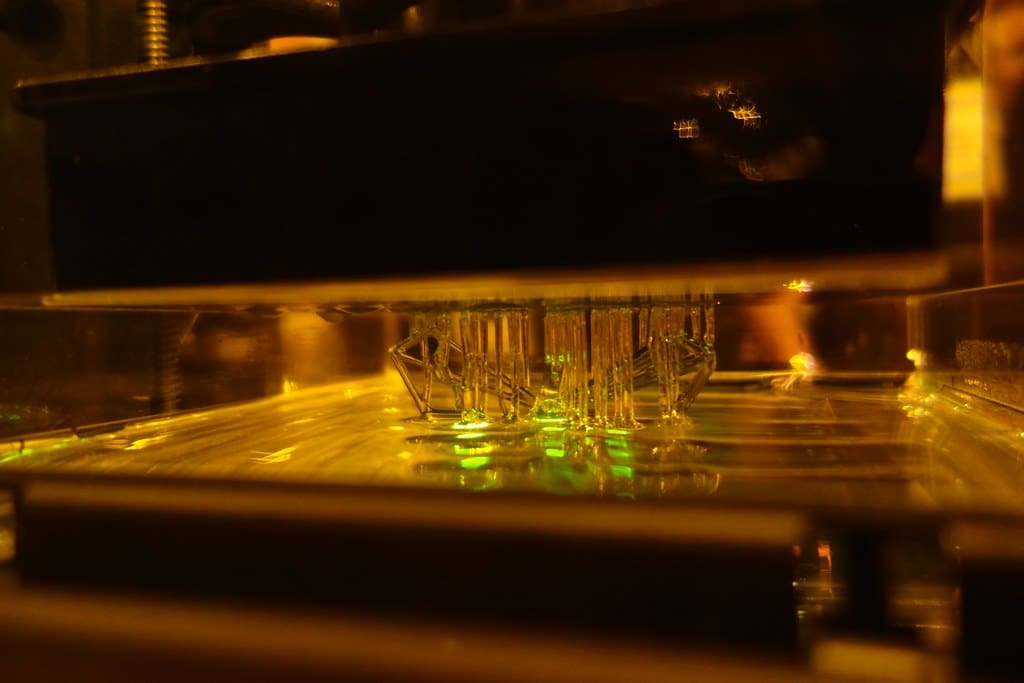
Selective Laser Sintering (SLS)
This method uses a laser to fuse small particles of polymer powder into a solid structure.
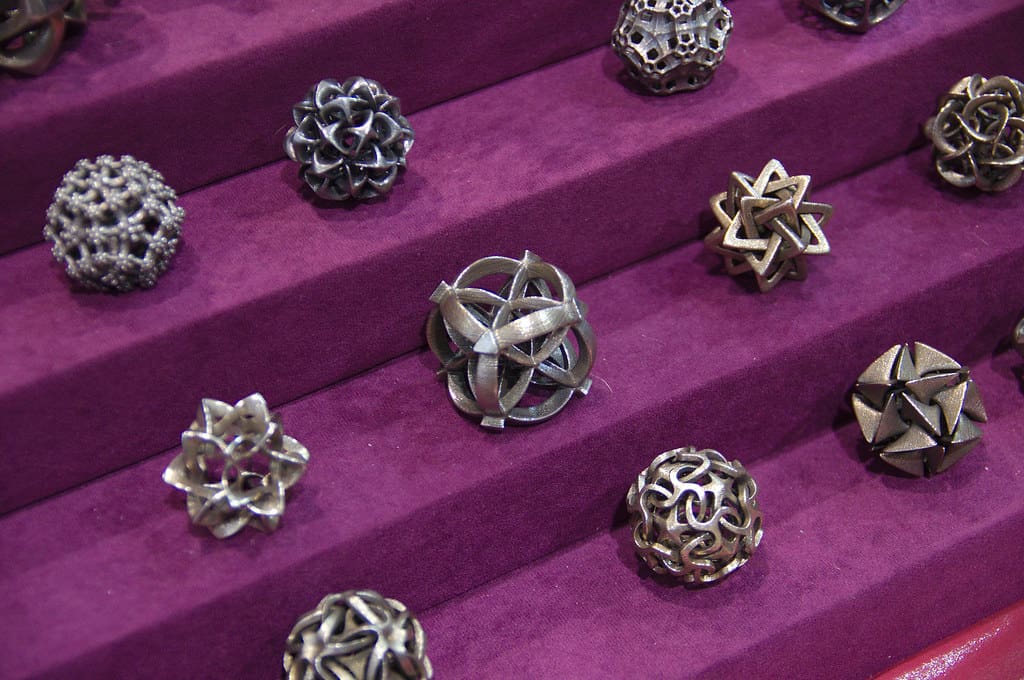
Digital Light Processing (DLP)
Similar to SLA, this method uses a digital light projector to flash a single image of each layer all at once, hardening the resin with much greater speed.
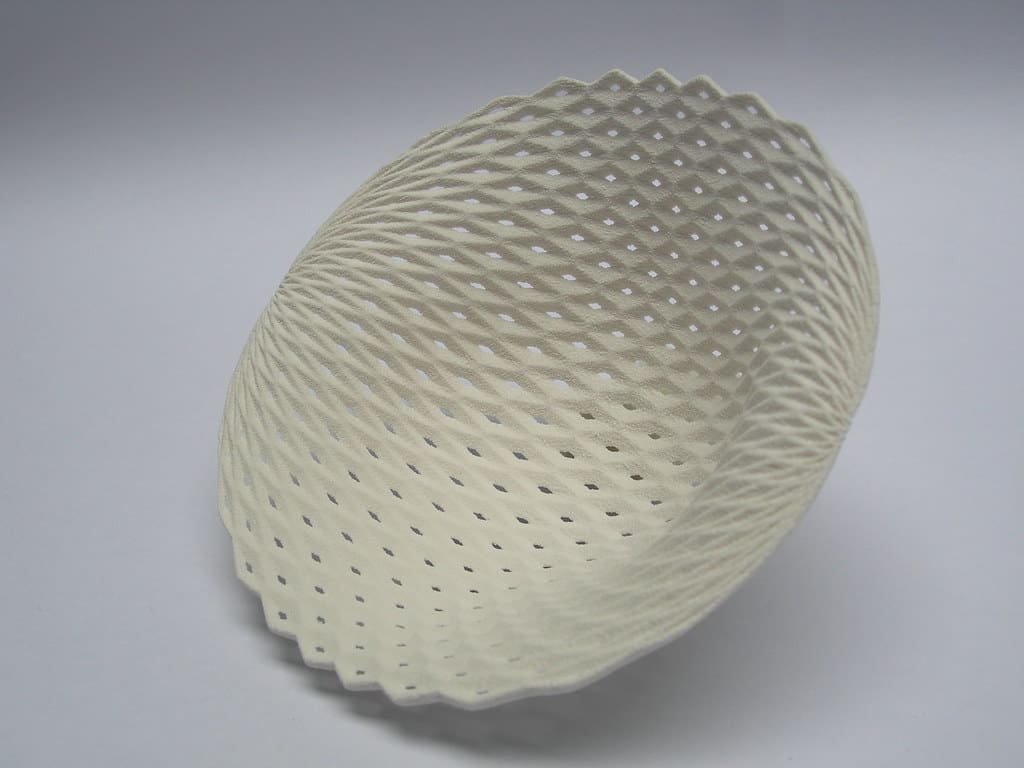
Binder Jetting
This method involves selectively depositing a liquid binding agent onto a layer of powder particles (be it metal, sand, or ceramic) to build an object layer by layer. After printing, the object may undergo post-processing steps like sintering or infiltration.
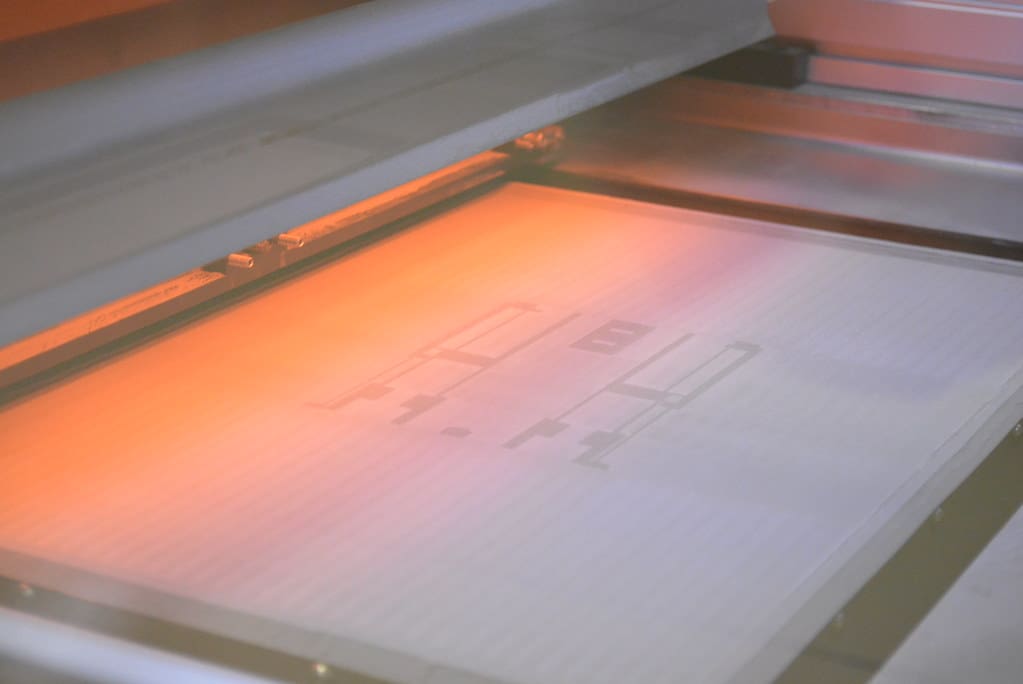
Each method uses different materials, ranging from plastics to metals and ceramics, allowing for flexibility in application. These technologies demonstrate the broad adaptability and potential of 3D printing across various industries and use cases.
Applications of 3D Printing
3D printing’s versatility has made it invaluable in many fields:
Medical: Prosthetics, implants, and even bioprinting tissues.
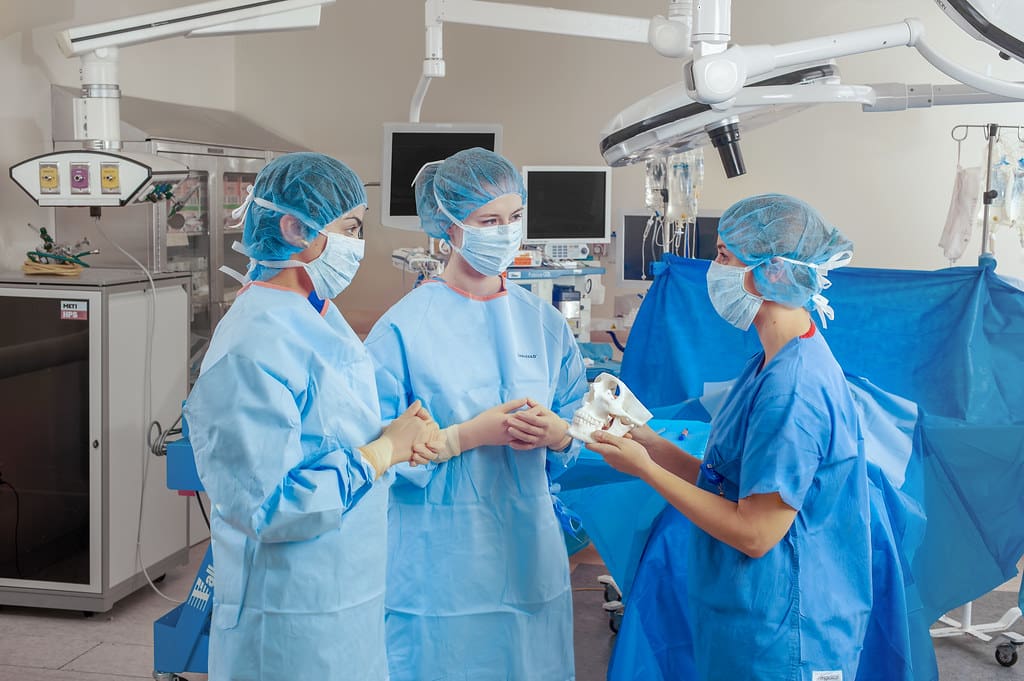
Automotive: Prototype models and functional parts such as dashboard panels.

Aerospace: Lightweight, complex parts for aircraft and spacecraft.
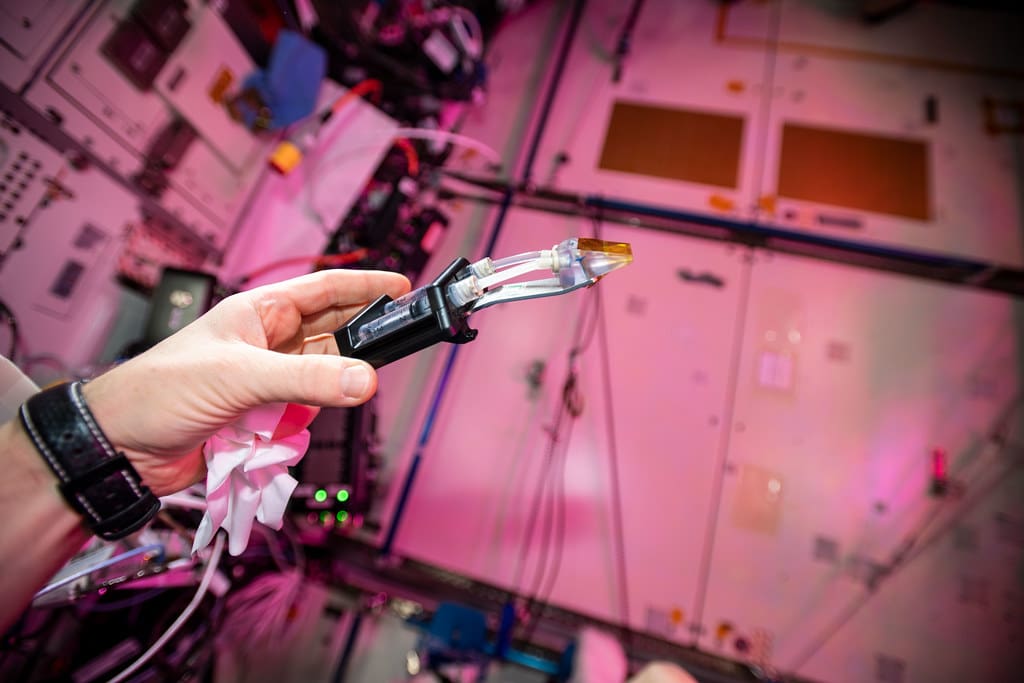
Consumer Products: Custom jewelry, home decor, and toys.
Product Development: 3D printing accelerates the product development cycle by allowing rapid prototyping. Designers and engineers can quickly create, test, and refine their concepts much faster than traditional manufacturing methods.
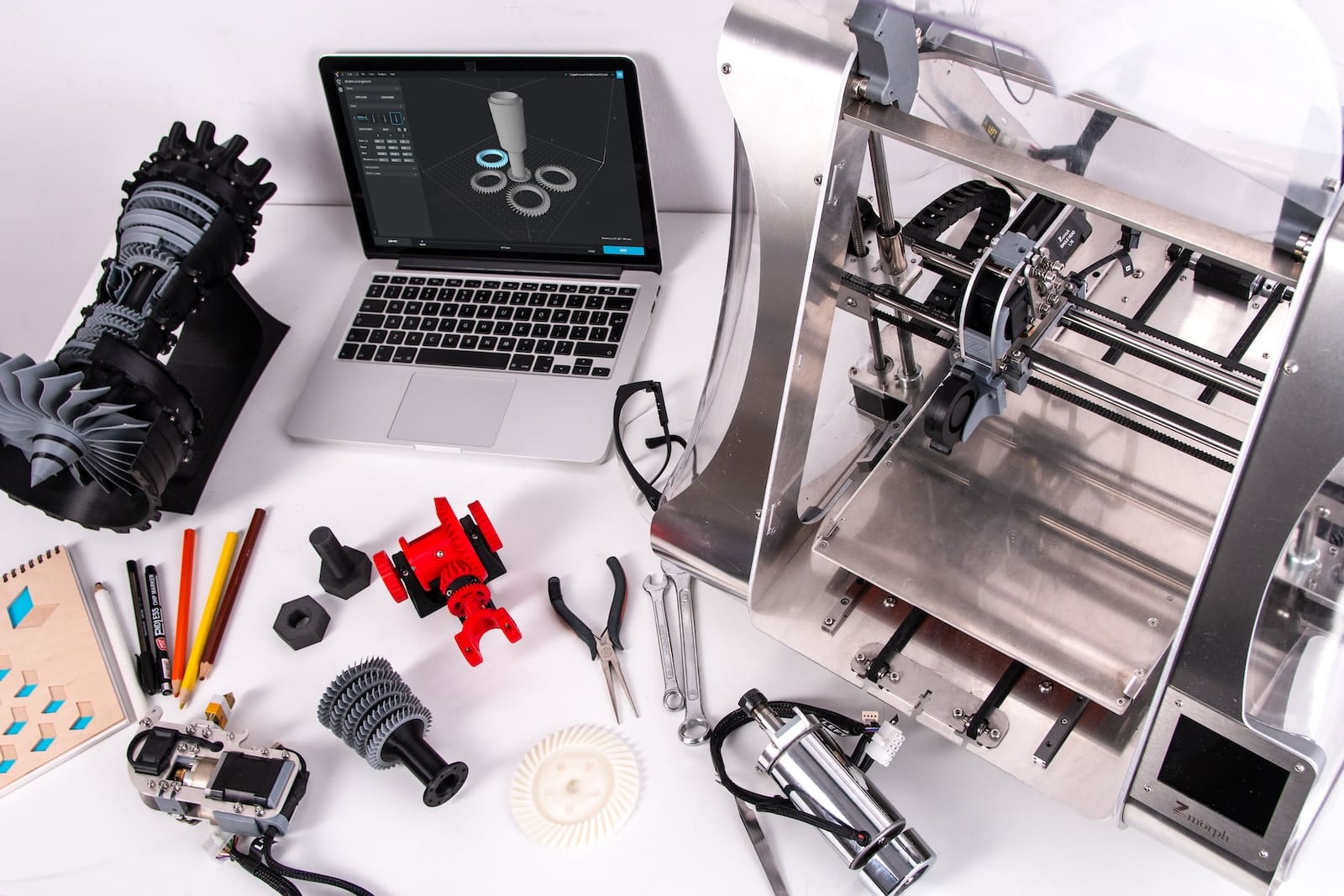
Education: Schools and universities increasingly incorporate 3D printing into their curriculums to enhance STEM education. It allows students to bring their ideas to life and learn about manufacturing and design principles hands-on.
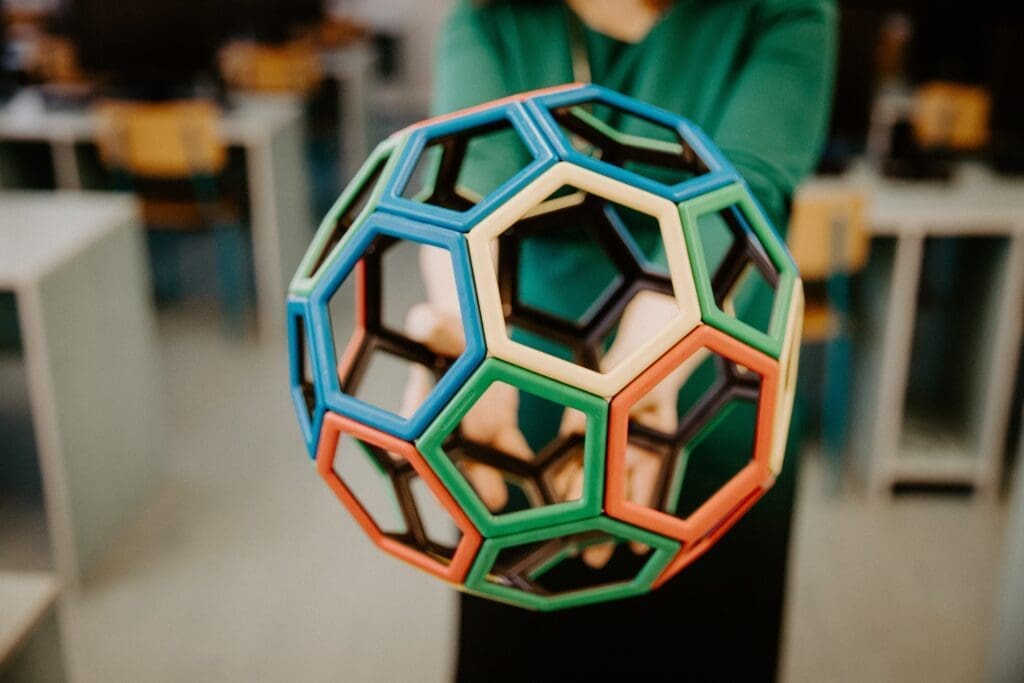
These applications demonstrate the wide-ranging impact of 3D printing, enabling faster development and more personalized production.
Advantages of 3D Printing
The benefits of 3D printing are significant:
Customization: Each item can be individually customized at no additional manufacturing cost.
Reduced Waste: Material is added layer by layer, reducing the waste commonly associated with traditional subtractive manufacturing.
Cost-Effectiveness: Reduces the need for expensive molds and tooling, making it cost-effective for small production runs and prototypes.
Challenges and Limitations
Despite its benefits, 3D printing faces challenges such as:
Speed: Slower production times compared to traditional manufacturing methods.
Material Limitations: Not all materials can be 3D printed, and those that can be often do not match the strength or durability of traditionally manufactured materials.
The Future of 3D Printing
The future of 3D printing promises even greater advancements with the development of new materials and methods. Innovations such as multi-material printing and increased speed are likely to open up even more applications, further integrating 3D printing into manufacturing processes and daily life.
3D printing is transforming industries by offering enhanced flexibility, reduced costs, and increased speed in prototyping and manufacturing. As the technology continues to evolve, its impact is set to grow, leading to more innovative applications and making the technology more accessible to all.