Selective Laser Sintering (SLS) is a powerful 3D printing technology that uses a laser to sinter powdered material, typically nylon or other polymers, layer by layer to form solid structures. Unlike other forms of 3D printing, SLS does not require support structures as the powder bed itself supports the object being printed. This capability makes SLS an excellent choice for complex geometries, including interiors, moving parts, and intricate details. Understanding the key components of an SLS 3D printer is essential for both optimizing its use and maintaining the equipment effectively. This post delves into the intricate system of an SLS printer, exploring each component’s function and its role in the printing process.
Core Components of an SLS 3D Printer
1. Powder Bed: The powder bed contains the raw material in powdered form that is used to create the 3D object. The powder not only acts as the medium for sintering but also supports the object during printing, eliminating the need for separate support structures. It is evenly distributed across the build area to ensure consistent layering and density.
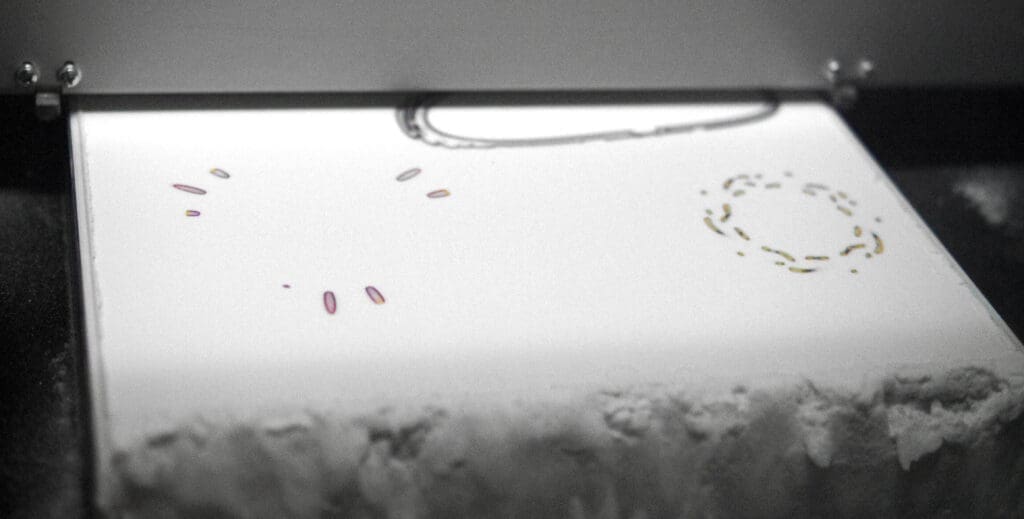
2. Powder Feed System: This system is responsible for supplying fresh powder to the powder bed. It typically includes a feed chamber adjacent to the build chamber, where fresh powder is stored and subsequently pushed onto the build platform. The precision of the feed system is crucial for maintaining an even layer of powder and ensuring the quality of the print.

3. Recoating Blade or Roller: After each layer is sintered by the laser, a recoating blade or roller spreads a new layer of powder over the build area. This component must be finely calibrated to ensure it applies a consistent and smooth layer of powder, which is essential for achieving the high resolution and surface finish that SLS is capable of.
4. Laser System: The laser in an SLS printer is the primary tool for sintering the powder. It selectively fuses powder particles together by scanning over the powder bed based on the cross-sections of the 3D model. The type of laser used, typically a CO2 laser, needs to deliver precise and controlled energy to achieve consistent sintering across the build area.
5. Galvanometer Scanners: Galvanometers are used to steer the laser beam across the build platform. They control the mirrors that reflect the laser, directing it with high precision. The accuracy and speed of the galvanometer scanners are vital for efficient printing processes and fine detail in the finished product.
6. Heating System: The entire powder bed is pre-heated to just below the melting point of the powder material. Maintaining a uniform temperature throughout the bed is crucial for successful sintering, as it prevents warping and ensures the structural integrity of the printed object. The heating system usually includes a combination of heaters around the build chamber.
7. Temperature Control System: This system monitors and regulates the temperature within the build chamber to ensure optimal printing conditions. Stable and precise temperature control is necessary to avoid inconsistencies in the sintering process, which could lead to defects in the final product.
8. Nitrogen Gas Supply: Many SLS printers operate under a nitrogen atmosphere to prevent oxidation of the powder during the sintering process. The nitrogen gas supply must be consistent and clean to maintain the chemical integrity of the materials and ensure high-quality prints.
9. Build Platform: The build platform in an SLS printer typically moves vertically, lowering after each layer is completed to allow the application of a new powder layer. The platform’s movement must be precisely synchronized with the recoating and sintering processes to maintain the correct focus and intensity of the laser on the surface of the powder bed.
10. Control Software and Interface: The software that controls an SLS printer translates digital models into instructions for the laser and adjusts parameters like laser speed, power, and focus. An intuitive user interface is essential for managing these settings and monitoring the printing process.
The components of an SLS 3D printer work together to produce robust, complex, and precise parts suitable for a wide range of applications, from functional prototypes to production parts. Understanding these components helps users to not only operate the machine effectively but also to maintain and troubleshoot it, ensuring consistent performance and long-term reliability. As SLS technology continues to evolve, further advancements in component efficiency and material capabilities are expected, which will expand the possibilities of what can be achieved with this innovative printing technology.