Structural engineering, a critical field within the civil engineering discipline, is undergoing significant transformation with the adoption of 3D printing technology. This innovative approach to construction offers the potential to revolutionize how buildings and other structures are designed, fabricated, and constructed. By allowing for greater design flexibility, efficiency, and sustainability, 3D printing is poised to change the landscape of structural engineering fundamentally.
The Emergence of 3D Printing in Structural Engineering
Originally utilized primarily for prototyping in various industries, 3D printing has increasingly been recognized for its potential in actual construction applications. In structural engineering, this technology facilitates the creation of complex geometrical structures that can be both aesthetically pleasing and functionally superior. The ability to print components directly from digital models not only speeds up the construction process but also reduces material waste significantly.
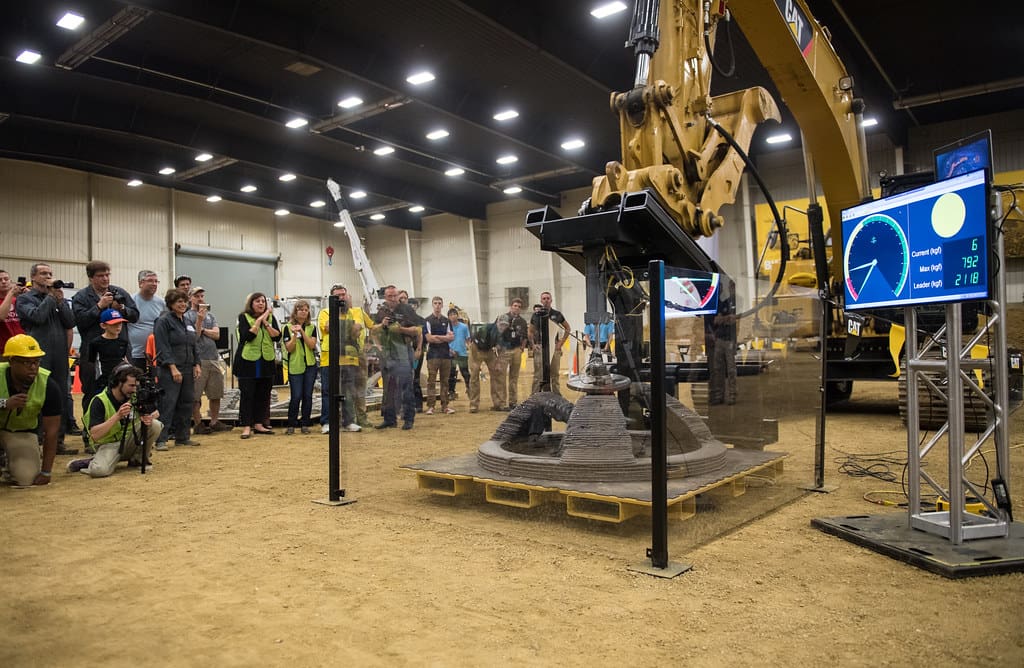
Advantages of 3D Printing in Structural Engineering
Innovative Design Capabilities: 3D printing allows structural engineers to push beyond traditional design boundaries. Complex designs that were once considered impractical or too expensive to build can now be realized. These include intricate load-bearing structures that optimize material usage and enhance the aesthetic appeal of buildings.
Increased Construction Speed and Efficiency: With 3D printing, components can be produced on-demand and assembled on-site, significantly reducing the time from design to completion. This rapid construction capability is particularly valuable in projects with tight deadlines or in disaster recovery situations.
Material Optimization and Sustainability: 3D printing contributes to sustainability in construction through efficient material use and the potential to utilize recycled materials. The precise layer-by-layer construction process minimizes waste, and the ability to create optimized structural elements can reduce the overall amount of material required.
Cost Reduction: The streamlined production process, reduced material waste, and decreased labor requirements associated with 3D printing can lead to significant cost savings in large-scale construction projects.
Key Applications of 3D Printing in Structural Engineering
Customized Concrete Structures: One of the most common applications of 3D printing in structural engineering is in the creation of customized concrete elements. Using concrete as a primary material, 3D printers can produce walls and other structural components tailored to specific architectural requirements.
Steel Fabrications: Advanced 3D printers are capable of printing with metals, including steel. This capability is particularly useful for creating complex, custom-fabricated steel connections and nodes, which are often critical in modern architectural designs.
Bridges and Overpasses: Several prototype bridges and overpasses have been successfully constructed using 3D printing technologies around the world. These structures demonstrate not only the feasibility of 3D printing for large-scale applications but also its potential to innovate traditional approaches to bridge construction.
Seismic Retrofitting: 3D printing offers new solutions for strengthening existing buildings to resist seismic forces. Customized retrofitting components can be designed and printed to fit specific buildings, enhancing their safety without compromising historical integrity.

Challenges in 3D Printing for Structural Engineering
Despite its advantages, several challenges need to be addressed to fully integrate 3D printing into mainstream structural engineering practices:
Material Durability and Performance: Ensuring the long-term durability and structural integrity of printed materials remains a primary concern. Ongoing research is needed to ascertain the performance of 3D-printed materials under various environmental conditions and loads.
Scale Limitations: While 3D printing is effective for small to medium-sized projects, scaling it to larger applications is still a technological and economic challenge. Current printer sizes and speeds may not be feasible for all types of large-scale structural engineering projects.
Regulatory and Code Compliance: The construction industry is highly regulated, and building codes have not yet fully adapted to include 3D-printed structures. Developing standards and obtaining approval for 3D-printed buildings can be complex and time-consuming.
Future Directions in 3D Printing for Structural Engineering
The future of 3D printing in structural engineering looks promising, with ongoing technological advancements and increasing recognition of its potential benefits. Continued development in printer technology, materials science, and digital design tools is expected to address current challenges and broaden the scope of 3D printing applications in structural engineering.
3D printing is set to revolutionize structural engineering by offering more flexible design possibilities, reducing construction time and costs, and promoting sustainable building practices. As the technology continues to evolve, it is likely to become an integral part of the structural engineering landscape, transforming how engineers design and build the structures of the future.