Reliability engineering focuses on ensuring that products and systems perform their intended function under specified conditions without failure, for a designated period. It is crucial across various sectors, including aerospace, automotive, electronics, and heavy machinery. 3D printing, also known as additive manufacturing, has become a vital tool in reliability engineering by allowing for the rapid prototyping, testing, and optimization of parts to enhance their reliability and durability.
The Emergence of 3D Printing in Reliability Engineering
Initially utilized for prototyping in design and manufacturing, 3D printing has expanded its applications to include the production of final parts that are used in critical functions within various industries. This shift is largely due to advancements in printing technologies and materials that meet the stringent requirements of reliability engineering. These advancements enable engineers to iterate designs quickly, test parts under real conditions, and improve products based on the insights gained.

Advantages of 3D Printing in Reliability Engineering
Rapid Prototyping and Iteration: 3D printing accelerates the design process by allowing for quick production of prototypes that can be immediately tested and refined. This rapid iteration helps in identifying potential failures and enhancing product reliability before full-scale production.
Customization and Complexity: Additive manufacturing enables the creation of parts with complex geometries that are often more durable and efficient than those made with traditional manufacturing methods. Such complexity can include internal structures designed to withstand specific stresses or channels for improved heat dissipation.
Material Innovation: 3D printing has spurred the development of new materials and composites that can withstand extreme conditions such as high temperatures, corrosive environments, or mechanical stresses, thereby enhancing the reliability of the components produced.
Reduced Waste and Cost: By using only the necessary material to create a part and enabling the integration of multiple functions into a single print, 3D printing reduces waste and lowers the cost of manufacturing, which is essential for extensive reliability testing.
Key Applications of 3D Printing in Reliability Engineering
Aerospace Components: In an industry where failure can have catastrophic consequences, 3D printing is used to produce parts that not only meet but exceed reliability standards. Components such as turbine blades, brackets, and satellite parts are printed to optimize weight and durability while being subjected to rigorous testing.
Automotive Parts: The automotive industry employs 3D printing to create parts that must withstand repetitive stress and variable environmental conditions. Components like engine parts, transmission components, and complex assemblies are prototyped and tested to ensure longevity and safety.
Electronic Housings and Enclosures: Protecting sensitive electronic components is critical for their reliability. 3D printing is used to create custom housings that fit precisely, provide adequate cooling, and protect components from mechanical shock, vibration, and electromagnetic interference.
Medical Devices: In the medical field, device reliability can directly impact patient health. 3D printing is used to produce surgical tools, implants, and prosthetics that not only fit perfectly but also perform reliably over time, often in bio-compatible materials that must endure the stresses of the human body.
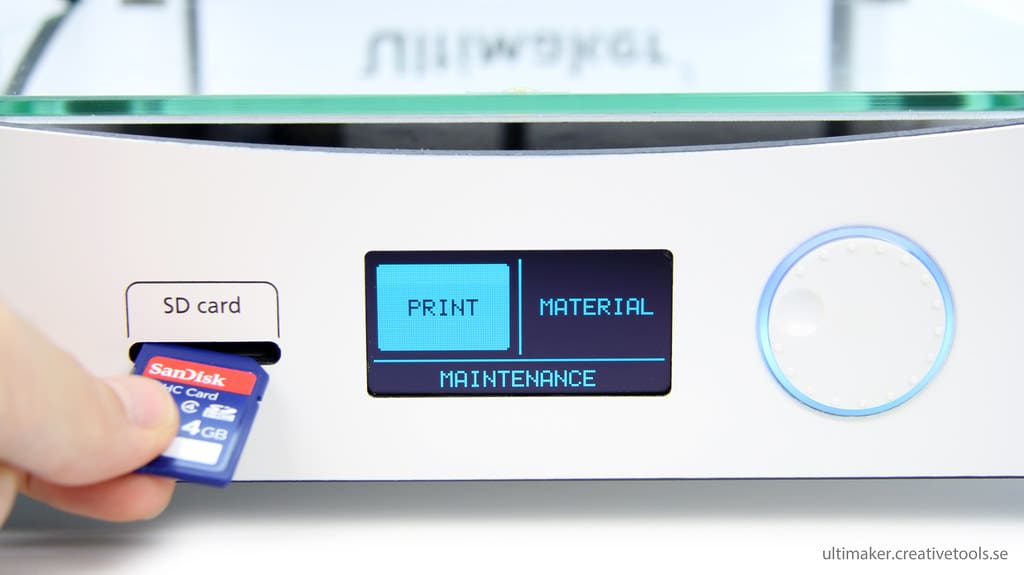
Challenges in 3D Printing for Reliability Engineering
Consistency and Standardization: Achieving consistent quality in 3D printed parts, especially across different machines and batches, is challenging. Standardization in printing parameters and material properties is critical to ensuring reliability.
Scale Production: While 3D printing is ideal for prototyping and small production runs, scaling up to large volumes can introduce variability that may affect the reliability of the parts.
Technical Expertise: Deep knowledge in both 3D printing technology and material science is essential to optimize designs for reliability. Engineers must understand the nuances of printer settings, material behavior, and post-processing methods to ensure parts meet strict reliability criteria.
Testing and Validation: Validating the reliability of 3D printed components often requires extensive and costly testing to ensure they meet the required specifications and standards, especially in heavily regulated industries.
Future Directions in 3D Printing for Reliability Engineering
The future of 3D printing in reliability engineering holds promising advancements in printer technology, materials, and software integration. Innovations in continuous fiber printing, high-performance polymers, and advanced metal printing techniques will further enhance the strength and durability of printed components. Additionally, AI and machine learning are expected to play a significant role in optimizing printing processes and predicting part performance under various conditions.
3D printing is revolutionizing reliability engineering by providing tools to enhance the design, testing, and production of reliable and durable components. As the technology continues to evolve, it will enable even more precise and efficient manufacturing solutions, pushing the boundaries of what is possible in reliability engineering. This progress promises to make products not only more reliable but also more innovative and suitable for future challenges.