Railway engineering is undergoing a revolutionary change with the adoption of 3D printing technology, also known as additive manufacturing. This innovative approach is altering how train components are designed, produced, and maintained, offering significant improvements in efficiency, customization, and sustainability. As the railway industry strives to enhance operational efficiency and passenger comfort, 3D printing emerges as a critical tool, enabling the rapid development and deployment of sophisticated railway solutions.
The Emergence of 3D Printing in Railway Engineering
Initially utilized for prototyping in various industries, 3D printing has expanded its reach to include the production of functional, end-use components in railway systems. This transition has been driven by advancements in 3D printing technologies and materials that meet the stringent requirements of railway operations, such as durability, safety, and longevity. Today, railway companies and manufacturers are embracing 3D printing not only to streamline production processes but also to revolutionize the design and maintenance of trains and railway infrastructure.
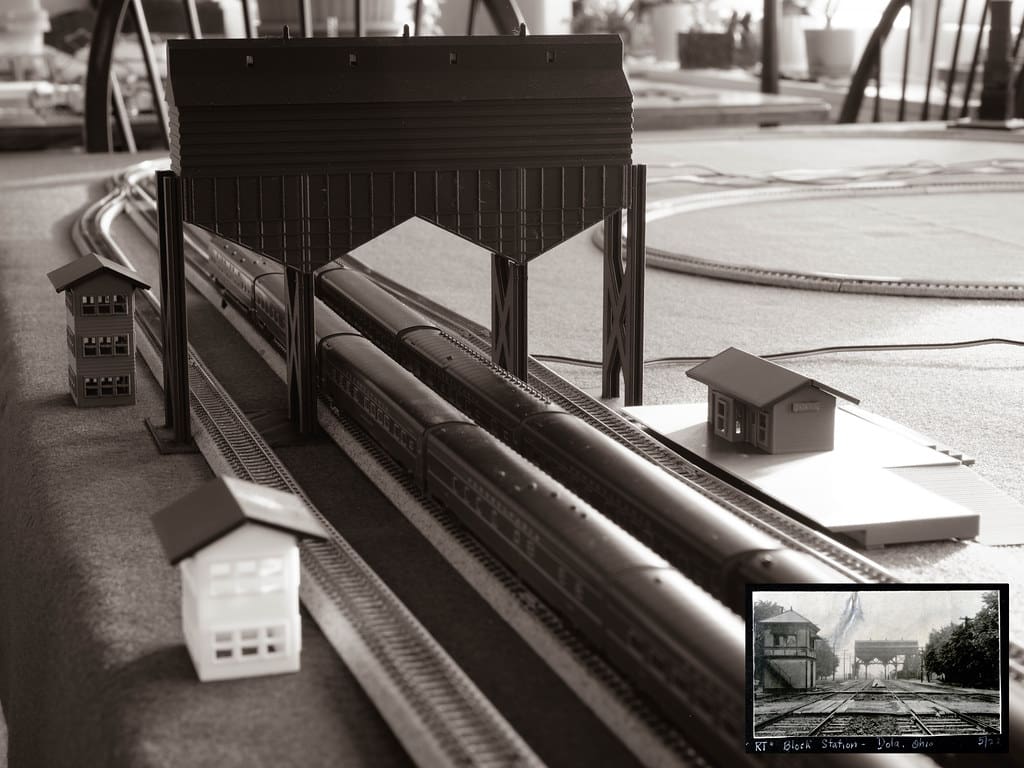
Advantages of 3D Printing in Railway Engineering
Customization and Flexibility: 3D printing allows for the creation of customized parts tailored to specific railway applications, from ergonomic seat designs to optimized mechanical components. This capability facilitates rapid adaptation to changing industry needs and passenger demands.
Complex Component Production: The technology excels at manufacturing complex components that are difficult or too costly to produce with traditional methods. This includes intricate parts for propulsion systems, lightweight structural components for carriages, and detailed fittings and fixtures that enhance passenger comfort.
Reduced Material Waste and Cost: Additive manufacturing minimizes waste by using only the material necessary to build a part, which is particularly important in an industry aiming to reduce its environmental footprint. Additionally, the ability to produce parts on-demand reduces the need for large inventories, lowering storage and logistics costs.
Improved Maintenance and Repair: 3D printing offers significant advantages in the maintenance and repair of trains by enabling on-site production of replacement parts. This drastically cuts downtime and enhances service reliability, as components can be produced and replaced more quickly than with traditional supply chains.
Key Applications of 3D Printing in Railway Engineering
Structural Components and Interiors: Train manufacturers use 3D printing to produce various structural parts and interior components, such as panels, brackets, and housing units. These parts often benefit from the lightweight and strong properties of advanced 3D printing materials.
Custom Cabins and Ergonomic Designs: Personalized cabin components, such as seats and handrails, are produced using 3D printing to improve ergonomics and passenger comfort. These designs can be easily modified to accommodate different trains or updated based on passenger feedback.
Prototyping New Technologies: Rapid prototyping capabilities of 3D printing allow engineers to develop and test new railway technologies quickly. This includes everything from energy-efficient systems to advanced safety features.
Tooling and Equipment Manufacturing: 3D printing is also utilized to create specialized tools and equipment needed for railway maintenance and operations. This not only speeds up repair processes but also ensures that maintenance staff have access to the best tools for specific tasks.
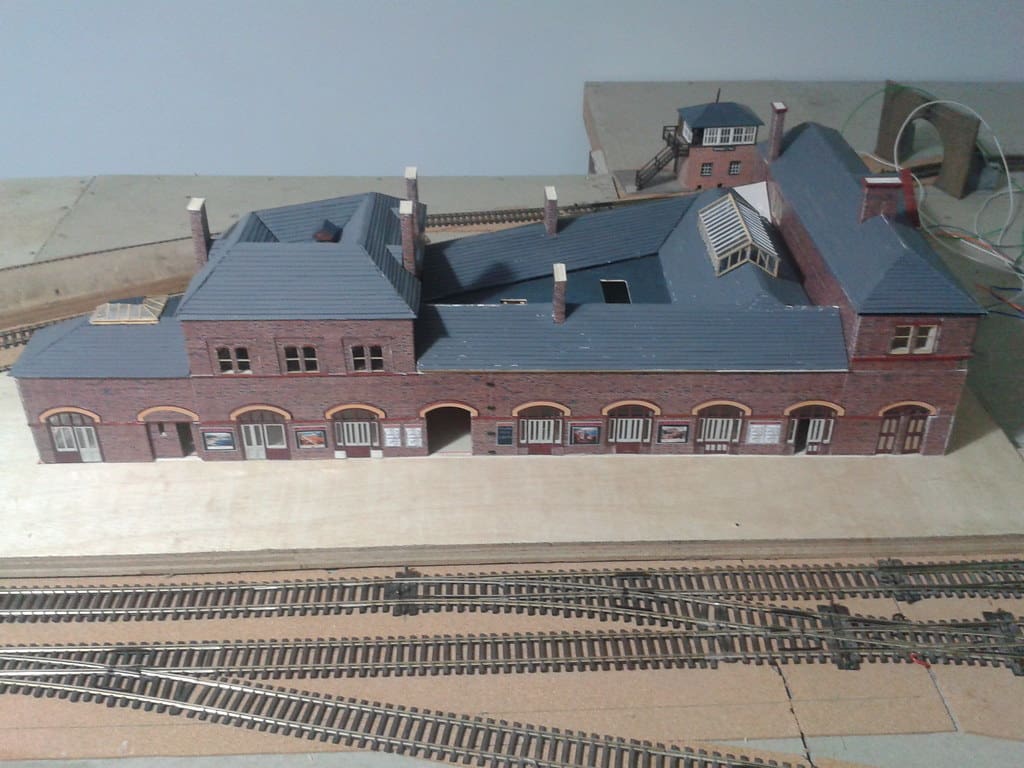
Challenges in 3D Printing for Railway Engineering
Despite its growing adoption, several challenges remain in the widespread integration of 3D printing within railway engineering:
Material Performance: Ensuring that 3D-printed materials meet the rigorous safety and performance standards required for railway operations is crucial. Materials need to withstand heavy loads, vibration, thermal extremes, and long-term wear and tear.
Regulatory Approval and Standardization: Achieving regulatory approval for 3D-printed railway components involves extensive testing and certification processes. Standardizing these procedures to facilitate broader adoption remains a complex challenge.
Scaling Production: While 3D printing is effective for prototyping and small production runs, scaling up to industrial quantities required for railway applications can be technologically and economically challenging.
Future Directions in 3D Printing for Railway Engineering
The future of 3D printing in railway engineering looks promising, with continuous advancements in printer technologies, materials science, and design software poised to overcome current limitations. As these technologies mature, 3D printing is likely to become an integral part of railway manufacturing and maintenance, leading to more innovative, efficient, and passenger-friendly railway services.
3D printing is set to continue its transformative impact on railway engineering, providing new levels of efficiency, customization, and innovation. As the technology evolves, it promises to reshape how trains are built and maintained, potentially leading to significant advancements in the speed, safety, and sustainability of rail transport.