Automation plays a pivotal role in modern manufacturing, offering efficiency, precision, and scalability that manual processes cannot match. The integration of 3D printing into automation systems has created a synergy that is transforming industrial production. Known for its ability to rapidly prototype and produce customized parts, 3D printing enhances automation by providing flexible manufacturing solutions, reducing lead times, and decreasing the cost of production.
The Emergence of 3D Printing in Automation
3D printing, or additive manufacturing, has progressed from creating simple models to producing complex, functional parts used in automated systems across various industries. This technology’s growth has been driven by its ability to fabricate parts on demand, its minimal setup requirements, and the continuous improvement in printable materials that meet industrial standards. As a result, 3D printing is increasingly integrated into automated production lines to create more adaptable and efficient manufacturing environments.
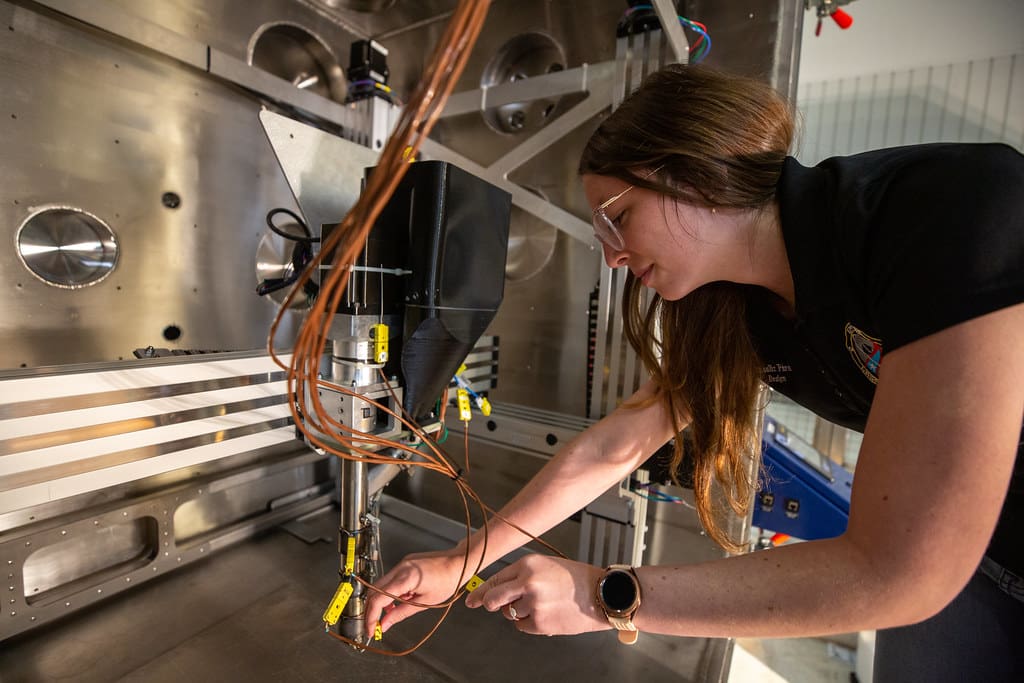
Advantages of 3D Printing in Automation
Design and Production Flexibility: 3D printing allows for the creation of parts with complex geometries that are often impossible to achieve through conventional manufacturing methods. This capability is especially beneficial in automation, where customized jigs, fixtures, and robot grippers are frequently required.
Reduced Time and Cost: By integrating 3D printing into automated systems, companies can significantly reduce the time and cost associated with the production of custom parts and small batches. There is no need for costly molds or extensive retooling, allowing for quick design changes and iterations.
Enhanced Innovation: 3D printing encourages innovation by enabling engineers to experiment with new designs and solutions without significant financial risk. This leads to better products and processes, as well as enhanced problem-solving capabilities within automated manufacturing.
Improved Supply Chain Efficiency: With 3D printing, components can be produced on-site as needed, simplifying logistics and reducing the dependency on external suppliers. This on-demand production capability is crucial for maintaining the efficiency of automated systems, especially in industries facing rapid product lifecycle changes.
Key Applications of 3D Printing in Automation
Custom Tooling and End-Effectors: Automated assembly lines often require specific tools that are tailored for particular tasks. 3D printing can produce these custom tools quickly and economically, including robotic end-effectors that are optimized for specific handling or assembly tasks.
Prototyping Automated Components: Before full-scale production, new automated machinery components can be prototyped using 3D printing. This allows for thorough testing and optimization, ensuring that the parts perform well under operational conditions.
Production of Final Parts: In some sectors, 3D printing is not just for creating prototypes but is also used for the final production of parts, especially those with complex designs or those that benefit from being lightweight, such as in aerospace and automotive industries.
Integration into Robotics: Robotics is a crucial element of modern automation systems, and 3D printing is used to create both the structural parts of robots and their intricate internal mechanisms. This includes everything from gears and bearings to entire robotic arms.

Challenges in 3D Printing for Automation
Material Limitations: While there have been significant advancements in printable materials, finding materials that can withstand the rigorous demands of automated industrial environments, particularly in terms of durability and thermal stability, remains a challenge.
Scale Limitations: For large-scale production, 3D printing is often not as efficient as traditional manufacturing methods. Balancing when to use 3D printing versus conventional processes is crucial for operational efficiency.
Quality Consistency: Ensuring consistent quality across 3D printed parts can be challenging, especially when scaling up production. Variability in printing can affect the performance of parts in automated systems.
Technical and Operational Integration: Integrating 3D printing into existing automation systems requires careful consideration of workflow, software integration, and training. The need for specialized knowledge and equipment can also pose barriers to implementation.
Future Directions in 3D Printing for Automation
As 3D printing technology continues to evolve, its integration into automation will likely become more profound and widespread. Future developments may include advances in the speed and quality of 3D printing, broader material options, and improved integration with existing manufacturing technologies. Additionally, the use of AI and machine learning could enhance the predictive capabilities of 3D printing processes, optimizing designs for automated production and real-time adjustment to manufacturing conditions.
3D printing is set to continue revolutionizing the field of automation, offering new levels of flexibility, efficiency, and customization. As this technology matures, it will enable more innovative, responsive, and cost-effective manufacturing solutions, fundamentally changing how products are designed, produced, and delivered. The ongoing advancements in 3D printing promise to further enhance its role in automation, making it an essential component of the modern industrial landscape.